Publication
Index:
Factory Visits, Data Collection, and Data Description
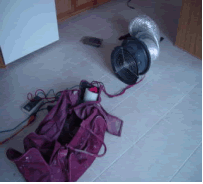 |
Figure
1.
Duct blaster used to test air tightness of duct systems
during factory visits. |
Factory
Visits
Data
and findings presented here were gathered during 39 factory
visits to 24 factories of six HUD Code home manufacturers
interested in improving the energy efficiency of their homes.
Researchers conducted tests on 101 houses representing 190
floors .
During
an initial factory visit, BAIHP researchers typically meet
with factory managers for an introduction to Building America
and the systems engineering approach to building better houses.
Factory managers explain their objectives, challenges they
are facing (call backs, reoccurring problem, etc), and conduct
a factory tour for BAIHP researchers. During the tour, researchers
observe assembly techniques and identify areas of potential
improvement.
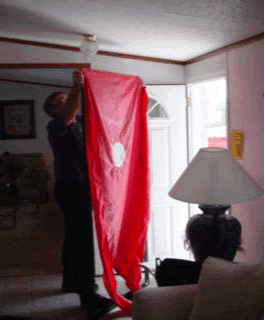 |
Figure
2. BAIHP Researcher Neil Moyer sets up blower
door for testing the air tightness of a manufactured house.
|
Researchers
test completed duct systems (Fig. 1) in the factory and in
finished houses (Fig. 2), if available, to assess initial
duct tightness. This creates a benchmark for gauging progress
as managers implement duct sealing and assembly recommendations.
After
the factory visit, BAIHP researchers provide the factory managers
with a Trip Report detailing the findings of the visit, including
test results, and making recommendations for improvements.
Recommendations may cover heating and cooling equipment efficiency
and installation, marriage line details, insulation installation,
infiltration and moisture control strategies, window specifications,
and duct system air tightening.
Duct
System Air Tightness
Duct tightening is among the most commonly recommended improvements.
It improves the indoor environment, durability, energy efficiency,
and comfort of the home simultaneously. (Appendix
B, Duct Leakage and House Pressure Concepts). The EPA
Energy Star Program for Manufactured Homes also requires that
duct leakage to the outside be reduced to below 3%, 5%, or
7% of the conditioned floor area (Qnout) depending on the
package of energy features selected (MHRA, 2001.)
Studies
in new and existing site built homes have documented that
duct leakage can be reduced to a Qnout of less than 5% by
sealing the joints with a combination of fiberglass mesh and
mastic.
A
compilation of findings from field studies around the country
shows average savings from air tight duct construction in
new and existing homes to be 15% cooling energy savings and
20% heating energy savings (Compilation of findings in Cummings,
et al, ‘91 and ‘93, Davis ’91, Evans, et
al, ‘96, and Manclark, et al ‘96.) Field repairs
in these studies were usually made using UL181 listed tape
and/or mesh and mastic.
Duct Sealing
Mastic is an elastomeric material specifically made for permanently
sealing the fabricated joints and seams in heating, cooling,
and ventilating ducts and thermal insulation. BAIHP recommends
the water based formulae for installer safety and easier cleanup.
Mastic is supplied in either buckets or tubes for application
with a brush, trowel, or caulk gun. Some preparations include
a fiber reinforcement component. The elastomeric properties
of mastic allows it to expand and contract as the dimensions
of the duct system change during each cycle of heating or
cooling.
Mastic
should be UL181 listed for the type of duct material/insulation
being sealed.
When sealing holes larger than ¼” a fiberglass
reinforcing membrane (mesh) is used to cover the hole and
form a bed for applying the mastic (RCD, 2003.) UL181 listed
tape may be used in lieu of the mesh. Generally, this size
hole does not occur in the factories after cutting quality
and component alignment has been improved.
The
longevity of mastic yields a performance advantage over tape.
Whereas taped systems may perform well initially, they may
become leakier over time if the adhesive fails due to material
movement at the joints surface and/or temperature differences
and changes. Mastic, on the other hand, tolerates the temperatures
differences between inside and outside the duct as well as
the frequent temperature changes over the life of the system.
These
savings and performance advantages are achieved at relatively
low first cost (see Economics of Duct Tightening for Manufactured
Housing, p. 19) compared to other energy improvements such
as equipment efficiency and window upgrades.
After
manufacturers have implemented BAIHP recommendations, researchers
may return to the factory for reassessment. Depending on the
success of implementation, additional recommendations and
reassessment are sometimes needed.
Duct
System Recommendations
Duct system recommendations discussed in this report include:
- Set
duct tightness target of Qn equal to or less than 6% total
and 3% to outside. Note that the ultimate real goal
is the latter target, 3% to outside. Conventional wisdom
estimates leakage-to-outside to be 50% of the total leakage.
Thus the 6% total target serves as a surrogate for leakage-to-out
when only leakage to outside can not be measured, such as
during production or before set up is completed.
-
Achieve duct tightness by properly applying tapes and sealing
joints with mastic and, when needed, fiberglass mesh
- Accurately
cut holes for duct connections
-
Fully bend all tabs on collar and boot connections
-
Trim and tighten zip ties on flex duct with a strapping
tool
-
Provide return air pathways from bedrooms to main living
areas
Data
Collection and Duct Tightness Goals
BAIHP duct system testing follows building science standard
test procedures using a calibrated fan (duct blaster) to depressurize
the duct system to a specific pressure, in this case 25 pascals
(pa). The amount of air in cubic feet per minute (cfm) needed
to achieve this pressure is determined, yielding a measure
of total system leakage at a standard test pressure. This
measure is referred to as CFM25total.
A
further test can be performed after the house is completed
by using another calibrated fan to simultaneously depressurize
the house and the duct system to the same pressure. This eliminates
air flow between the two, yielding a meaure of system leakage
to the outside at the same standard test pressure. All duct
leakages measured during this test involves air from outside
the conditioned space. This measure is referred to as CFM25out.
A low leakage to the outside is generally the ultimate objective
since leakage to the house is considered much less detrimental
to air quality, durability, comfort, and energy efficiency.
To have “substantially leak free ductwork”, BAIHP
recommends keeping system leakage to the outside below a CFM25out
measurement equal to 3% of the conditioned floor area (Qnout).
However,
the CFM25out test can not be performed until the house is
nearly finished. Researchers and factory staff need to assess
duct system tightness during production, when the duct system
is still accessible for repair if needed. Based on the assumption
that only a portion of the total leakage will be lost to the
outside, duct tightness goals for production are set in terms
of total leakage, CFM25total, typically 6% of conditioned
floor area (Qntotal) as illustrated in the following example.
Determining
Duct Tightness Targets Example: |
For
a house of conditioned area = 1800 ft2 |
Target
Total Duct Leakage: |
(CFM25total)
= (1800 ft2)(6%) = 108 cfm |
Target
Duct Leakage to Outside: |
(CFM25out)
= (1800 ft2)(3%) = 54 cfm |
Continue
to Observations >>
|