Publication
Index:
Observations
Researchers
find variation among manufacturers related to duct system
materials, layout, fabrication, assembly, sealing, quality
control and air handler position. The primary distinction
focused on in this data set is the duct sealing method. Researchers
tested 132 floors with mastic sealed duct systems and 58 floors
with taped duct systems (Table 1). Depending on the stage
of production and the objective of the testing, researchers
measured total leakage only, leakage to the outside, or both.
Table
1 Characteristics of Data Set |
|
Taped |
Mastic |
Total |
Factories
Visited |
|
|
24 |
Total
Visits |
|
|
39 |
Manufacturers |
|
|
6 |
Number
of Tests |
Total
Floors |
58 |
132 |
190 |
CFM25Total
Tests |
56 |
124 |
180 |
CFM25Out
Tests |
30 |
86 |
136 |
Type
of Test Conducted |
CFM25Total
Only |
30 |
44 |
74 |
CFM25Out
Only |
4 |
6 |
10 |
Floors
Tested for Both |
26 |
80 |
106 |
Duct
Layout
Ducts systems observed in these tests were installed either
in the attic (ceiling systems) or in the belly (floor systems).
Perimeter floor systems have a main supply duct with smaller
run-out ducts extending to the edges of the house. In-line
floor systems have a main supply duct that is directly connected
to supply registers with floor boots.
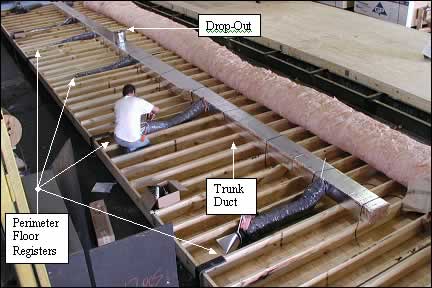 |
Figure
3. Duct assembly stations become a focus of improvement
and quality control when factories strive to meet to qualify
for Energy Star. Photo shows perimeter floor duct system
with flex duct runs from duct board trunk to registers.
Note this floor assembly will be flipped over after insulation
is completed. |
Occasional
a “baby duct” will be run to serve a room that
doesn’t intersect the main supply trunk, such as a master
bath or a laundry room. The data set represents a mixture
of ceiling and floor systems, both perimeter and in-line layout,
as summarized in Table 2.
Table
2 Duct Location and Layout in Data Set |
|
Taped |
Mastic |
Total |
Undocumented |
1 |
0 |
1 |
Overhead
Systems |
25 |
44 |
69 |
Floor
Systems |
32 |
88 |
120 |
Floor Perimeter |
2 |
8 |
|
Floor Inline |
1 |
34 |
|
Floor Undocumented |
29 |
46 |
|
Total
Systems Tested |
58 |
132 |
190 |
Air
Handler Position and Connection to Duct System
Heating and cooling systems are either package units or split
systems.
In
homes designed for package systems, a duct drops
from a central return plenum through the belly into the crawl
space for connection to the package unit during set-up. The
supply ducts, one from each section of the house, have a similar
drop into the belly for connecting to the package unit. Thus,
each section is directly connected to the main supply trunk.
In overhead duct systems, this connection is sometimes made
in the attic during set-up.
In
homes designed for split systems, an air handler
with a central return is installed during production. If the
house is a multi-section unit with floor ducts, a drop-out
collar is installed near the air handler in each trunk duct
for tying the non-air handler section(s)’s supply ducts
into the air handler. These are connected during set using
a cross over duct (flex duct) in the crawl space for floor
systems. Multi-section overhead systems are often connected
through the attic during set-up.
Multiple
returns are rare. Through-the-wall grills are sometimes used
to provide a passive return air path from bedrooms.
Researchers have observed that the HUD Code requirement of
1in2 of return air area for every 5ft2 of
floor area served is not always adequate to prevent the main
body of the house from depressurizing when bedroom doors are
closed. BAIHP highly recommends adequate return air provisions
to all bedrooms using passive, through wall grills or ducting
from bedroom ceiling to main body ceiling.
Duct
Materials
Manufactures typically install ducts made of sheet metal,
duct board, and flex duct.
Duct
board components which are generally assembled in the
factory include supply ducts, return plenums, ceiling boots,
distribution boxes, etc.
Flex
ducts are used in conjunction with prefab sheet metal
collars to connect duct board components. Flex ducts are secured
to collars with plastic zip ties. Collars are secured to duct
board with built in tabs that fold out around the edge of
the duct board.
Sheet
metal components, such as floor boots are generally pre-fabricated
by suppliers in standard sizes. Sheet metal trunk ducts are
fabricated in the factory. Table 3 summarizes the duct materials
represented in the data set.
Table
3 Duct Materials in Data Set |
|
Taped |
Mastic |
Undocumented |
5 |
0 |
Sheet
Metal with Flex |
24 |
22 |
Duct
Board with Flex |
29 |
110 |
Total
Systems Tested |
58 |
132 |
Continue
to Challenges to Achieving Duct Tightness Recommendations
>>
|