ABSTRACT
A
significant number of new manufactured houses
built to HUD code and located in the hot, humid
Southeast are experiencing moisture problems.
Soft wallboards, buckled floors, damaged wood
molding and extensive mold growth are the most
common symptoms. These problems do not respond
to the standard service and repair strategies
for water intrusion
At
the request of four manufacturers, over twenty-five
such moisture damaged homes were investigated
in 1999 and 2000 to determine likely causes.
One time blower door, duct tightness and pressure
differential measurements were performed on all
homes. Field data on ambient, crawlspace, belly
and house temperatures and RH were collected on
a few of the homes. Recommendations and reports
were prepared for the manufacturers service, production
and design staff. Field repairs were performed
in most of these homes.
A
generalized theme existed in the houses investigated.
·
Lowered air conditioner thermostat
setting (typically 68-73oF),
below the ambient dew point.
·
Negative pressures across
the envelope from high supply duct leakage
(cfm @25Pa > 10 per 100 square feet of conditioned
floor area), inadequate return air paths, interior
door closures, exhaust fans or a combination
thereof.
·
Inadequate moisture removal
from disconnected return ducts, fans always
on (air handler or ventilation), inadequate
drainage of condensate, oversized air conditioner
or a combination thereof.
·
Moisture diffusion from
the ground into the house because of poor site
drainage, inadequate crawl space ventilation,
tears in the belly board, or a combination thereof.
·
Vapor retarder in the wrong
location i.e. vinyl or other impermeable
wall or floor coverings located on the colder
surfaces.
Recommended
solutions provided to the manufacturers to eliminate
moisture problems include:
·
Maintain air conditioner thermostat
above the ambient dew point (at least 75oF
)
·
Eliminate long term negative
pressures created by air handler fans or ventilation
equipment.
·
Tightly seal all ductwork and
provide adequate return air pathways.
·
Enhance moisture removal from
the conditioned space by correct sizing and
maintainence of equipment
·
Eliminate ground source water
and provide adequate moisture barrier for the
floor assembly
·
If possible, remove vapor barriers
located on the wrong surfaces.
Work
is continuing to determine if these steps will
be sufficient to prevent problems even in the
presence of vapor barriers in the wrong locations
for the hot, humid climates that are preferred
by manufacturers and customers.
INTRODUCTION
Of
the two million homes built in the U.S. in 1999,
over 18.5% were built in factories to the code
of the U.S. Housing and Urban Development (HUD).
In 2000, one out of six new single-family housing
starts were manufactured homes. Last year, the
industry shipped 250,550 homes from 280 manufacturing
facilities. Over 19 million people, about 8 percent
of the U.S. population, live full-time in over
8 million manufactured homes (Manufactured Housing
Institute 2000a). These manufactured homes are
one of the most affordable single family detached
housing available any where in the world, generally
costing less than $35/ ft2 plus land
costs for centrally air conditioned and heated
homes with built in kitchens. Available in all
parts of the country, manufactured homes are more
popular in the southern and western U.S. where
land is still plentiful and in rural areas elsewhere.
In
1999, the U.S. Department of Energy (DOE) competitively
selected the Florida Solar Energy Center (FSEC)
as the Building America Industrialized Housing
Partnership (BAIHP) team leader. This groups
primary function is to serve the manufactured
housing industry by fostering technology-based
innovations that will increase energy efficiency
through a systems engineering of the whole house.
The systems engineering approach considers the
interaction between the building site, envelope,
and mechanical systems, as well as other factors.
It recognizes that features of one component in
the house can greatly affect others and it enables
the teams, including the manufacturers and suppliers,
to incorporate energy-saving strategies at no
extra cost. System trade-offs, like the tightened
shell that enables an engineer to recommend a
smaller HVAC system, can improve the quality and
performance of a home without affecting its first
cost to the builders or to the consumers. The
BAIHP team has three specific objectives in mind
while serving the industry:
1.
Cost effectively reduce the heating,
cooling and hot water energy usage of industrialized
housing and portable classrooms by up to 50%
while enhancing indoor air quality, durability
and manufacturing productivity.
2.
Assist in the construction of thousands
of energy efficient industrialized houses annually.
This goal is acomplished by touring production
facilties to try and pin-point problem areas
and work with the manufacturers to resolve the
problems, and provide design assistance.
3.
Make our team members pleased and proud
to be working with us.
Industrialized
housing includes manufactured housing (built to
the HUD code), modular housing (factory built
housing modules assembled on site) and production
housing (site built housing produced in a systematic
manner). Currently, there are five HUD-code manufacturers
that are BAIHP team members. These include:
·
Cavalier Homes
·
Clayton Homes
·
Fleetwood Homes
·
Palm Harbor Homes
·
Southern Energy Homes
The
driving force that has encouraged these builders
to become team members varies from builder to
builder, however there is a general underlying
theme. A number of their homes built for the
hot and humid climate (built according to HUD-code
specifications) have experienced various degrees
of building failure due to moisture. A
subtask of the effort with the DOE Building America
Program is entitled Moisture Research.
In this endeavor, FSEC will attempt to help team
members to eliminate moisture problems plaguing
HUD Code homes in the Southeast by
conducting
diagnostic tests in problem homes, fixing problem
homes, evaluating the effectiveness by conducting
pre/post fix short term tests, and related activities
The
HUD-Code Home
What
is the difference between a manufactured home,
a modular home and a panelized home? Many types
of structures are built in a factory and designed
for long-term residential use. Manufactured and
modular home units are built in a factory, transported
to the site location and installed. Panelized
and pre-cut homes, essentially flat units (factory-built
panels or factory-cut building materials) are
transported to the site location and assembled.
The major difference is that manufactured homes
are federally regulated by the HUD Code under
Title 24 CFR 3280. The HUD Code provides the
design and construction requirements for the complete
production of the entire home in the factory,
with some modifications permitted for on-site
completion. Modular, panelized and pre-cut homes
fall under the auspice of the model building code
enforced in the jurisdiction where the home will
be located. These codes can include the BOCA
National Building Code, the ICBO Uniform Building
Code, the Southern Standard Building Code or the
ICC One- and Two-Family Dwelling Code.
The
Construction Process and Setup
The
process of constructing a manufactured home is
very different from the conventional site built
home the home is built from the inside
out as it travels down an assembly line. A steel
chassis is constructed and the floor assembly
(containing plumbing, wiring, and duct work) is
attached. Floor coverings, interior walls, plumbing
fixtures, and furnace are installed. The exterior
walls with the interior finish and insulation
are hoisted into place and attached to the floor.
The finished ceiling assembly is then lifted from
the construction jig and lowered onto the home
(figure 1).
As exterior sheathings and coverings are attached,
a flurry of interior activities continues within
to provide finishing touches. The newly constructed
assembly is then moved to the operational test
site where the various plumbing and electrical
systems are checked.
Figure
2 shows a typical HUD-code home just produced leaving
the factory. These homes have a permanent steel
chassis with axles attached below the floor.
After production the homes could travel a few
hundred miles, hauled by a truck, before set up
in its final location. The homes are set upon
blocks or piers and the steel frame chassis is
firmly anchored to the ground. A vented skirting
conceals the underside of the home.
The
Duct System
Manufactured
homes are typically heated or cooled by a forced
air system employing ductwork, which delivers
hot or cold air from the air handler unit (AHU).
The ductwork may be located in the attic or in
the belly cavity of the home. Figure
3 shows the ducts in the belly, supplying
conditioned air to all rooms through floor vents.
This is a very common and inexpensive system that
is used in manufactured homes. The ducts are
typically made out of aluminum or fiberglass trunk
lines which supply air to the floor registers
through in-line boots or through flex ducts, which
terminate to perimeter registers on the floor.
The most common method of sealing the various
joints and connections is with a foil tape.
Multi-section
homes will also have a section of the ductwork
that is connected during the setup operation.
A flexible duct is used to connect the supply
sections together in the attic or in the crawlspace.
These connections are usually made with duct tape
and/or a tie strap. (Note: the authors have seen
three out of twenty-five instances during the
course of this project where there has been complete
or nearly complete separation of this connector
duct.)
The
Ventilation System
All
HUD-code homes are required to have a ventilation
system installed. Title 24 CFR Part 3280.103b
Light and ventilation states that
Each
manufactured home shall be capable of providing
a minimum of 0.35 air changes per hour continuously
or at an equivalent hourly average rate. The
following criteria shall be adhered to.
Natural
infiltration and exfiltration shall be considered
as providing 0.25 air changes per hour.
The
remaining ventilation capacity of 0.10-air
change per hour or its hourly average equivalent
shall be calculated using 0.035 cubic feet
per minute per square foot of interior floor
space. This ventilation capacity shall be
in addition to any openable window area.
The
remaining ventilation capacity may be provided
by: a mechanical system, or a passive system,
or a combination passive and mechanical system
.
Currently,
there are two main types of ventilation systems
that are employed by the manufacturing housing
industry to meet the 0.10 air change per hour
requirement. Both types are used in the hot and
humid climate; an exhaust only system that is
located in a hallway or utility room and an outside
air supply system that is ducted from the roof
to the return airside of the air handler fan.
The exhaust ventilation system is manually controlled
with a simple on-off switch. The outside air
supply system is linked to the operation of the
air handler and controlled with an automatic damper
(if applicable).
MOISTURE
PROBLEMS IN MANUFACTURED HOMES
Moisture
problems are being experienced by a significant
number of manufactured homes in the hot, humid
climate of the Southeast United States. According
to the Manufactured Housing Research Allaince
(MHRA), solving moisture problems is the highest
research priority of the HUD code industry. Moisture
problems (Figure 4)
include extensive mold, soft wallboards, buckled
floors, damaged wood molding and trim, and high
relative humidities in the home. Frequently,
these homes have a high air-conditioning bill
as homeowners attempt to increase comfort by lowering
the thermostat temperature. (Note: each degree
F drop in temperature causes an approximate 10%
increase in cooling costs. The BAIHP team has
investigated over 25 problem homes and has found
that the problems are caused by the following
factors acting individually or in combination
·
Lowered air conditioner thermostat
setting (typically 68-73oF), well
below the ambient dew point.
·
Negative pressures across
the envelope from high supply duct leakage
(cfm @25Pa > 10 per 100 square feet of conditioned
floor area), inadequate return air paths, interior
door closures, exhaust fans or a combination
thereof.
·
Inadequate moisture removal
from disconnected return ducts, continuous operation
of air handler or exhaust fans, inadequate removal
of condensate, oversized air conditioner, poorly
maintained equipment or a combination thereof.
·
Moisture diffusion from
the ground into the house because of poor site
drainage, inadequate crawl space ventilation,
tears in the belly board, or a combination thereof.
·
Vapor retarder in the wrong
location i.e. vinyl or other impermeable
wall or floor coverings.
Building
Science Basics For Moisture Plagued Homes
In
the hot and humid Southeastern U.S., the outside
air is consistently above a dewpoint of 75oF
during the summer months. If the homeowner decides
to keep the interior temperature of the home below
75oF, in an effort to maintain comfort,
or if an interior surface is cooled below the
exterior dewpoint temperature, then when moisture-laden
outside air comes into contact with cold inside
surfaces, condensation occurs. If it condenses
behind an impermeable surface such as vinyl flooring
or vinyl wallpaper, wall board damage, floor buckling
problems and mold problems can result. There
are six main sources that we have seen in our
investigations of ~25 problem homes with moisture
damage of unknown causes.
Interior
Temperature Below Outside Dewpoint (100% of the homes investigated)
Homeowners
want to be comfortable in their homes. Thermal
comfort is, in a simplified form, a function of
the temperature, humidity and the physical activity
of an individual (Fanger 1972). In most homes,
the only control feature is that of
the thermostat. The common perception is that
lowering the temperature will provide the cooling
comfort desired. The HVAC supplier/installer
wants to ensure that the homeowner has a unit
that is oversized to prevent callbacks of high
interior temperatures or home owner precieved
excessive run-times of the air conditioning system.
Oversizing can cause several problems that are
detrimental to the house and occupant comfort
(Karg, R. and Krigger J. 2000).
·
The unit is not operating long
enough to provide dehumidification. Dehumidification
is acomplished by passing return air over the
cooling coil.
·
The interior house temperatures
can be lowered to a point far below the ambient
air temperature dewpoint. This can lead to
condensation on interior surfaces, with its
attendant material degradation and mold growth.
Typical summer dewpoint temperatures range between
70 and 80 degrees F for most of the hot, humid
South, especially near coastal regions.
·
The oversized unit has a larger
blower fan, which exacerbates duct leakage and
pressure differential problems associated with
the forced air system.
Negative
pressures across the envelope (100% of the homes investigated)
Negative
pressure is the driver that brings warm moist
exterior air into the building through every crack,
crevice, hole or opening that exists. The negative
pressure field may encompass the entire building
or there may be zones within the building that
experience negative pressures created by inadequate
return air paths, or interior door closures. For
example, supply duct leakage and/or exhaust fans
may create negative pressures in the entire house,
while door closure may create negative pressure
in a single room or zone of the house. It is
important to note that we are talking about miniscule
amounts of negative pressures on the order
of 1 to 3 Pascals. However, over time, even these
tiny air pressures can lead to serious damage
(Odom, 1996).
Duct
leaks and return air pathways (100% of the homes investigated)
One
of the biggest causes of moisture problems in
manufactured homes, in hot and humid climates,
is leakage from the supply ducts. In manufactured
housing, the leakage is often caused by poor design
and construction practices which leaves holes
at the connection points of the AHU to the main
trunk, the boots (or risers) to the trunk, the
boots to the supply registers, end caps, cross-over
duct connections and other connection points in
the duct work. When the AHU moves air, some of
it leaks into the belly and eventually to the
outside through tears in the belly board. This
loss of air creates a negative pressure inside
the house and a positive pressure in the belly
as schematically shown in figure
5. The negative pressure draws outside
or attic air into the house through the numerous
cracks and crevices connecting the inside of the
house to the outside or the attic. If this outside
air is cold and dry, like it is in the wintertime
in the Northern U.S. it will increase the heating
energy use and occupant discomfort. This situation
would not rot the home in this climate but it
will in the hot, and humid Southern U.S..
Another
aggravating factor is the lack of return air transfers
when interior doors are closed. In many manufactured
and site built homes there is a single return
located in the main body, e.g. living room, dining
room, central hallway, of the house. Air returning
from individual rooms can be restricted by door
closure. There is often very little area provided
for return air from closable rooms; typically
this pathway is the undercut at the bottom of
the doors. When interior doors are closed, the
bedrooms become pressurized and the main body
of the house depressurizes. Figure
6 shows the pressure differential effect
of duct leakage and inadequate return air pathways.
House #10 shows a postive pressure because of
a disconnected main return air duct; that house
operates nearly 9 Pascals positive when the air
handler fan cycles on. The typical manufactured
home experiences supply only type leakage as the
return grill is normally located on the air handler
unit.
Exhaust
fans (8% of the
homes investigated)
Negative
pressures can also be created by the use of exhaust
fans. Whole house ventilation fans installed
in HUD code housing are designed to be able to
continuously exhaust air from the house at a rate
of at least 0.035 cubic feet per minute per square
foot of interior floor space. These fans are
operated by manually switching them on or off
(24 CFR Part 3280.103). In our inspections, we
noted only one home where the factory installed
ventilation fan ran continuously and it
suffered moisture problems (house #4). Typically,
this fan is not operated because of the noise
that it creates. Another case (house #16) we
investigated involved the installation of a dual
fan window unit. The owners converted a bedroom
into a pet care room and operated the window fans
to control odor. Unfortunately, this not only
removed the pet odor, but also depressurized the
entire house by 1 Pascal. High dewpoint crawlspace
air was pulled into the floor assembly through
numerous penetrations in the belly board and entered
the home via the plumbing, electrical and other
penetrations that existed in the floor. The result
was mold growth in the bathroom cabinets and the
deterioration of the subfloor under the kitchen
vinyl.
Inadequate
moisture removal (~80% of the homes investigated)
Proper
sizing, operation and maintenance of the air conditioning
system is necessary to maintain interior temperatures
and provide humidity control. It appears that
there may be a fair degree of oversizing of equipment,
though not specifically analyzed. Houses #19
and #20 are the same size, model, manufactured
in the same plant and are located a short distance
apart, yet one has a 4-ton air conditioning system
and the other only a 2.5 ton. Both experienced
problems, however the one with the larger unit
had a more severe moisture problem. Based on
the comments of the homeowners, some of the units
have the ability to lower interior temperatures
as much as 30 degrees below the ambient exterior
temperature. Anecdotally, we may say that if
the unit is capable of such a temperature difference,
then the unit is probably oversized. An oversized
unit will tend to short cycle, lowering the interior
temperatures, but not able to adequately remove
moisture from the air. In an effort to be comfortable,
the thermostat setting is lowered.
Excessive
duct system leakage also prevented adequate moisture
removal from the house. The air conditioning
systems were overwhelmed with ambient humidity
conditions. Three houses that were investigated,
had a portion of the duct system that was completely
disconnected. One (house #9) had a return duct
that had failed and was pulling the majority of
its air from the crawlspace. A second one
(house #3) experienced a disconnected crossover
supply duct. The majority of the conditioned
air was lost to the attic space. The third home
(house #16) had had the supply duct connecting
the package air condition system to the house
fall off at least three times within the first
few months after being installed.
Maintenance
and operation of the equipment also impacted the
moisture levels within the home. The thermostat
of house #4 was not operating correctly and the
air handler fan was always on. Operation of the
blower with supply leakage and door closure continuously
placed the home in a negative pressure of -1.0
Pascal. The home had had the interior wallboard
of all exterior walls replaced within the first
year of occupancy due to moisture damage. The
repair crew could not find the cause of the problem,
so the damaged wall was replaced, only to fail
again.
Blockage
in condensate drain line appears to have been
the final element needed to cause catastrophic
floor and wall damage to house #11. The homeowner
reported that the house had operated adequately
for the first year. They reportedly kept the
thermostat between 78-80oF and were
fairly comfortable. All at once the home felt
uncomfortable and the thermostat setting was lowered
to compensate, failure of materials and mold growth
soon followed. During our investigation, a pie
tin and plastic wrapper was found in the drain
pan of the evaporator coil of the unitary system.
The plastic wrapper was effectively blocking the
condensate drain line causing flooding of the
cabinet and recycling of the water back to the
house.
Moisture
diffusion through floor assembly (100% of the homes investigated)
It
appears in these homes inspected that one of the
moisture diffusion pathways existed between the
earth and floor coverings. The typical barrier
between the earth and floor coverings on a manufactured
home is a belly board. When these
belly boards have numerous penetrations or holes,
free passage of both air and water vapor into
the floor cavity now become an issue of concern.
In many cases, standing water, or evidence thereof,
existed in the crawlspaces below the belly boards.
A skirting that is designed to hide the crawlspaces
and provide attractive appearances then surrounds
these high moisture sources. [Note: a standard
for skirting ventilation of the area under the
home is to provide openings that have a net area
of at least one square foot for each 150 square
feet (Fleetwood Homes (1999) & Palm Harbor
Homes (2000)) [1] ]. Leaving warm, moist air no
choice but to rise up through the tears and other
openings of the belly boards into the subfloorings.
(This may be the result of air transported moisture
or moisture vapor diffusion or both.) The subfloorings,
composed of either plywood or wood composite materials,
allow moisture vapor to pass through to the floor
coverings. Carpeted surfaces offered little resistance
and moisture passes into the home; vinyl floor
coverings, on the other hand, are impermeable
surfaces and prevent moisture intrusion. If that
surface is at or below the dewpoint temperature
of the crawlspace air, then condensation occurs
on the underside of the impermeable flooring creating
favorable environments for mold growth.
There
appears to be a pattern of floor moisture/staining
problems when the duct system is located overhead
in the attic. Staining and warping of vinyl-covered
floors has occurred in areas under the register.
The areas of the vinyl covered flooring showing
the worst staining were being washed by cold air
from the supply registers (figure 7
& 8). Though measurements
were not made of floor temperatures, it stands
to reason that areas being washed by the supply
air will tend to be cooler than those areas not
washed. This cooling of the surfaces creates
temperatures below the crawlspace dewpoint temperature
and condensation occurs.
Vapor
retarder in the wrong location (100% of the homes investigated)
The
homes inspected followed the HUD code ruling on
moisture vapor control as defined by section 504,
which states
3280.504 Condensation control
and installation of vapor retarders.
(a)
Ceiling vapor retarders. (1) In Uo
Value Zones 2 and 3, ceilings shall have a vapor
retarder with a permanence of not greater than
1 perm (as measured by ASTM E-96-93 Standard
Test Methods for Water Vapor Transmission of
Materials) installed on the living space side
of the roof cavity. (2) For manufactured homes
designed for Uo Value Zone 1, the vapor retarder
may be omitted.
(b)
Exterior walls. (1) Exterior walls shall
have a vapor barrier not greater than 1 perm
(dry cup method) installed on the living space
side of the wall, or (2) Unventilated wall cavities
shall have an external covering and/or sheathing
which forms the pressure envelope. The covering
and/or sheathing shall have a combined permeance
of not less than 5.0 perms
.
(Note:
Uo Zone 1 includes Texas, Louisiana, Mississippi,
Alabama, Georgia, South Carolina, and Florida.)
It
is common practice for the manufacturers to use
a vinyl covered wallboard as the interior finished
surface. This is one of the most economical finishes
that can be applied and meets the vapor barrier
requirement. Testing of the wallboard with the
vinyl finish has been completed by others according
to the ASTM E-96 standard . The results of the
test showed that a 3/8 gypsum wall board
laminated with 4-mil vinyl has a perm rating of
0.42 (gr./hr.-ft3-in. Hg) (Manufactured
Housing Research Alliance 2000).
All
of the homes inspected that experienced wall board
failure were vinyl coated. Typical symptoms included
staining of the vinyl wallcoverings and bowing
of the wallboards. Additionally, negative air
pressures within the buildings were created by
duct leakages, door closures or a combination
of both.
The
vinyl floor coverings also fall into this category.
The vapor retarder is located on the interior
surface. The difference is that the problem has
only been seen in houses with overhead duct systems.
It is believed (testing to verify is still ongoing)
that the cool air from the supply registers is
being blown down to the floor and is cooling the
surfaces below outside air dewpoints. At this
point, the solution has been to replace the current
uni-directional registers with a multi-directional
one. Additionally, the belly board is also sealed
to prevent crawlspace vapor intrusion.
FIELD
TESTING
Currently,
more than 25 homes with moisture problems have
been field tested by BAIHP researchers and were
accompanied by the various manufacturers
service managers and other interested parties.
Table 1 provides observed and measured data from
several homes. The homes investigated are generally
located within 25 miles of the Atlantic Ocean
or Gulf of Mexico, ranging from North Carolina
to Texas (figure 9).
All of the homes have had at least one extensive
changeout of moisture damaged building materials,
many have had two or three.
Testing
Equipment and Procedures
FSECs
testing protocol employs a battery of tests to
establish the integrity of the building envelope
and the duct system. These tests assist in the
determination of the potential for air transported
moisture problems that can cause severe damage
to building components, increase energy consumption
and decrease occupant comfort. Ideally, the protocol
begins with three tests using a calibrated blower
door and a calibrated duct tester.
The
first test employs the calibrated blower door
and establishes a leakage rate for the house at
a specific pressure differential. This is usually
expressed in cubic feet per minute at 50 Pascals
(CFM50) or air changes per hour at 50 Pascals
(ACH50). The next two tests establish duct system
airtightness. These tests use the duct tester
and yield the leakage rate of the duct system
in a similar manner to the building air-tightness
test and are expressed in cubic feet per minute
at 25 Pascals (CFM25). One test measures the
total leakage from the duct system to the interior
and exterior of the building (CFM25total)
by pressurizing the duct system to 25 Pascals.
The second test measures leakage to the exterior
of the building only (CFM25out) by
pressurizing the building and the duct system
to the same pressure, removing any driving force
for leakage between the building and the duct
system. This results in the remaining leakage
being to the outside of the building envelope.
The results are airflow at 25 Pascals (cfm @ 25
Pa) and air leakage at 25 Pa normalized by the
conditioned house square footage (cfm/ft2 @ 25
Pa). A duct system to be considered to be essentially
leak free in the BIAHP project when the
normalized duct leakage to the outside is less
than 0.03 cfm/ft2 and the normalized total duct
leakage is less than 0.06 cfm/ft2.
[2]
The
testing protocol continued with a series of pressure
differential measurements across the building
envelope and across various zones within the building
as defined by interior doors. A digital micromanometer
with a resolution of 0.1 Pascal was used in all
of the pressure differential measurements. Pressure
differences may be created by either normal operation
of the buildings heating and cooling equipment,
ventilation system or exhaust fan (including clothes
dryers). Measurements were completed to determine
a magnitude and direction of flow across the envelope
when the various fans operate. Interior door
closure effect was also measured when the air
handler fan operated. Ideally, the pressure differentials
created across the building envelope and bedroom
doors should be fairly close to neutral.
Results
of Field Investigation
Since
the beginning of the moisture investigations in
the BAIHP project, it was the desire of this team
to try and determine the commonality that may
have existed. It appears that there is a common
thread that links moisture related failures and
the HUD code house of today.
There
are a number of similarities that existed in the
buildings that we inspected for the four manufacturer
team members:
·
All located in Southeast and
generally located within thirty miles of a large
body of water, either the Atlantic Ocean or
the Gulf of Mexico.
·
All had a forced air distribution
system that would generally considered to be
oversized. Most had duct leakage that was significant
and caused the building to operate in a negative
pressure.
·
Most of the homeowners kept the
thermostat setting between 68 and 75 degrees
F in an effort to maintain comfort.
·
Either a vinyl wallcovering or
a vinyl floor product was associated with the
moisture problem.
·
All of the homes have had at
least one major retrofit to repair the damaged
areas. Since a cause of the problem was not
located, the replaced materials were the same
as those that were removed.
·
Ventilation systems were usually
not used or disabled.
·
Typically, the master bedroom
door was closed for extended periods of time.
Usually, other bedroom doors were also closed
especially at night if children were
present.
·
The belly board (vapor retarder)
contained numerous holes, penetrations and tears.
The typical repair or seal was with the use
of an adhesive backed cloth tape (duct tape)
which had failed.
Table
1 identifies some of the characteristics
of the homes and symptoms observed. In general,
the investigation team was dealing with a homeowner
that has a problem, sometimes severe, and data
was gathered to identify the cause or source of
the problem. This limited time at the house caused
the focus to be on solutions and not necessarily
research, though an effort was exerted to have
a common data collection protocol.
SUMMARY
AND DISCUSSION
The
BAIHP investigation team was usually called out
to homes that were not able to be solved by the
normal channels that existed through the manufacturers
service departments. All of the problems that
were encountered related to moisture flow in a
vapor state. The causes of failure varied slightly
from house to house, but in general could be catorigized
as a result of any or all of the following:
·
manufacturing design and/or techniques
·
set-up and installation of non-factory
items such as air conditioning and
·
homeowner operation and maintainence
It
appears that moisture damage to the building materials
was a result of poor design criteria and workmanship
of a building that is located in a hot and humid
climate. There were some symptoms that were common
in cases:
·
Lowered air conditioner thermostat
setting (typically 68-73oF), well
below the ambient dew point.
·
Negative pressures across the
envelope from high supply duct leakage (cfm
@25Pa > 10 per 100 square feet of conditioned
floor area), inadequate return air paths, interior
door closures, exhaust fans or a combination
thereof.
·
Inadequate moisture removal from
disconnected return ducts, continuous operation
of air handler or exhaust fans, inadequate removal
of condensate, oversized air conditioner, poorly
maintained equipment or a combination thereof.
·
Moisture diffusion from the ground
into the house because of poor site drainage,
inadequate crawl space ventilation, tears in
the belly board, or a combination thereof.
·
Vapor retarder in the wrong location
i.e. vinyl or other impermeable wall or floor
coverings.
Recommended
solutions provided to the manufacturers to eliminate
moisture problems include:
·
Maintain air conditioner thermostat
above the ambient dew point (at least 75oF
)
·
Eliminate long term negative
pressures created by air handler fans or ventilation
equipment.
·
Tightly seal all ductwork and
provide adequate return air pathways.
·
Enhance moisture removal from
the conditioned space by correct sizing and
maintainence of equipment
·
Eliminate ground source water
and provide adequate moisture barrier for the
floor assembly
·
If possible, remove vapor barriers
located on the wrong surfaces.
One
of our manufacturing team members has been working
for the last five years in incorporting the best
practice designs and techniques into their product.
The result is that last year they reported no
moisture vapor related failures for the first
time in several years.
Work
is continuing to determine if these steps will
be sufficient to prevent problems even in the
presence of vapor barriers in the wrong locations
for the hot, humid climates that are preferred
by manufacturers and customers. There is still
much to done in the area of moisture research
as it relates to the interactions of buildings
and its mechanical systems. Negative pressures
created by mechanical systems within buildings
is sometimes difficult at best to correct. Obviously,
tight, well constructed duct systems with adequate
return air pathways is a giant step in the right
direction. There are still issues with ventilation,
especially exhaust only ventilation in the hot
and humid climates. Currently the HUD code does
not address the type of ventilation, only that
it must exist. Clothes dryers are another mechanical
exhaust device that exists in a great number of
homes. What is the effect of long term operation
in a home where it may operate three to six hours
per day? The industry, especially the HUD code
manufacturing industry is slow to change
change costs money. They are looking for ways
to lower manufacturing costs and still provide
affordable housing.
Education.
HUD code manufacturers, suppliers, retailers,
setup crews, and various code officials struggle
with moisture related problems, especially those
problems caused by moisture in the vapor form.
Good, simple and to the point training materials
and courses are needed to assist in the design,
construction, operation and diagnostics as it
relates to moisture and moisture movement mechanisms.
The
Building America Industrialized Housing Partnership
will continue working with manufacturers, suppliers
and building officials in an effort to provide
research, training and support.
TABLES
Table
1 Collected Data From 25 HUD Code Homes With Moisture
Related Problems
FIGURES
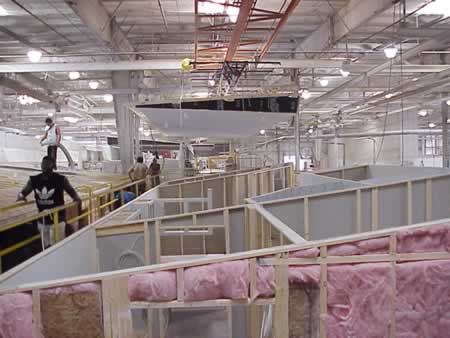
Figure
1 - Finished ceiling assembly being transferred
to the house. This assembly will be fastened to
the exterior walls with screws. At this point,
the floors, plumbing, duct system and electrical
wiring rough-ins are complete
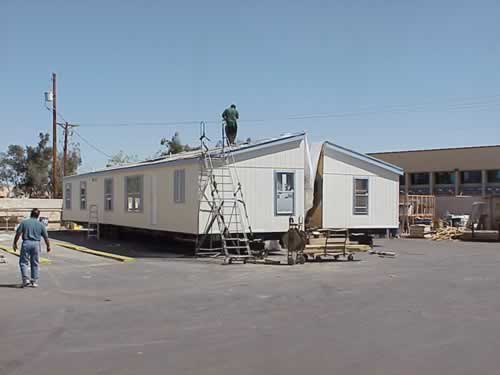
Figure
2
- A finished house in the function test area.
The plumbing and electrical systems are tested,
final touch-ups are completed and the home is
readied for transport.
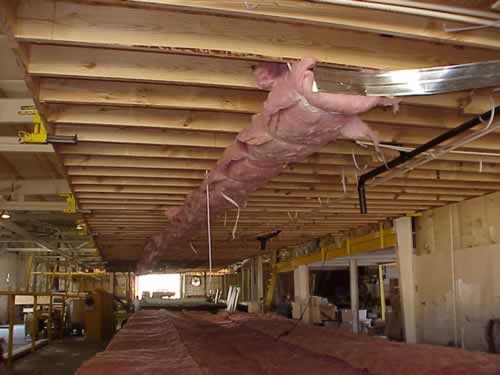
Figure
3 -
A finished metal inline duct
system. Insulation on the ductwork may or may
not be installed, depending on final destination
of the home. This floor is currently being lowered
onto the chassis
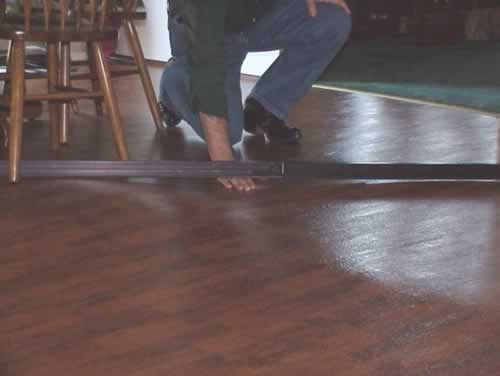
Figure
4
This home is experiencing
a buckled floor problem. The subfloor is a HUD
code approved composite wood product that has
taken on moisture from the crawlspace.
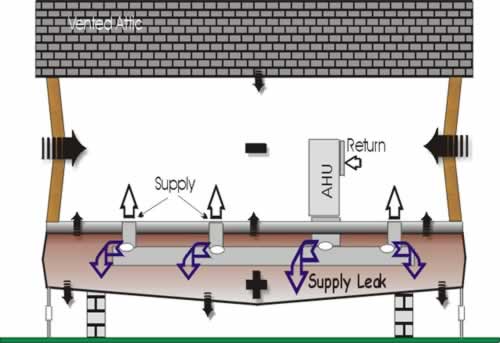
Figure
5 A typical manufactured house with an inline
floor supply system loses 10-30% of the air to
the "belly" of the home. There are usually
numerous holes, penetrations and tears in the
"belly" board, which allows free air
movement between the crawlspace and the "belly".
The loss of the supply air tends to depressurize
the living space above.
Figure
6
Pressure differential measured across the front
door when the air handler fan is operating and
all of the interior bedroom doors are open and
then closed. The main body or area containing
the central return experiences a negative pressure
with reference to outside.
Figure
7 Breakfast nook with a vinyl floor covering and
overhead supply register. Visible discoloration
of the floor (pink spots) existed primarily in
the area between the table and the cabinets on
the right side of the picture. The supply register
was oriented as to blow air to the outside wall.
Figure
8 The floor covering has been partial removed.
The plywood flooring was wet to the touch and
staining exists on much of the under side of the
vinyl. The floor decking was removed to inspect
the underside it appeared dry.
Figure
9 The southeastern portion of the United States
is considered to be a hot and humid climate.
The investigations that the BAIHP team has completed
are indicated. Note that most are near coastal
areas.
REFERENCES
Manufactured
Housing Institute (2000a), Quick Facts,
The latest Trends in Manufactured Housing 2000-2001,
2101 Wilson Blvd. Suite 610 Arlington,
VA 222013062
Odom,
J.D. and DuBose, G., (1996) Preventing Indoor
Air Quality Problems in Hot, Humid Climates: Problem
Avoidance Guidelines, CH2M Hill, Orlando
24
CFR Part 3280, DEPARTMENT OF HOUSING AND URBAN
DEVELOPMENT [Docket No. FR-4376-P-01] Manufactured
Home Construction and Safety Standards
Fanger,
P.O. (1972), Thermal Comfort, McGraw-Hill, New
York, USA
Karg,
R. and Krigger J. (2000), Specification of Energy-Efficient
Installation and Maintenance Practices for Residential
HVAC Systems, Consortium for Energy Efficiency,One
State Street, Suite 1400, Boston, MA 02109-3507
Fleetwood
Homes (1999), Installation Manual, Multi
Section, Wind Zone II & III, Fleetwood
Enterprises Inc., PO Box 76387638, Riverside,
CA 92513-9953
Palm
Harbor Homes (2000), Installation Manual,
Palm Harbor Homes Inc., 15303
Dallas Parkway, Suite 800, Addison, TX 75001
Manufactured
Housing Research Alliance (2000), Manufactured
Housing Technologies, Volume 2 Issue 2,
2109 Broadway, Suite 200, New York, NY 10023
|