II.
BAIHP Technical Assistance (D-E)
- Dukane
Precast
Naperville, Illinois
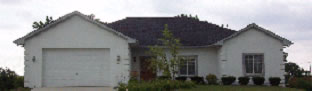 |
Figure
13 Completed
Dukane
Precast home tested by BAIHP |
FSEC
made a February 2002 site visit to Dukane Precast in Naperville,
Illinois and provided technical design assistance in
a follow-up telephone conference call in March ‘02.
In
2003, Dukane Precast requested BAIHP assistance in the
design phase and monitoring of the first prototype of a
new line of homes called “The Fortified
House (Figure
13). Objectives of Dukane’s Fortified
House include energy efficiency, comfort, durability,
and good indoor environment conditions.
In December 2003, FSEC visited 3 prototype buildings
in various stages of construction in. One was complete.
Researchers made recommendations regarding window flashing,
below grade drainage and waterproofing, interior ducts,
air sealing, attic access detail, floor finishes with
radiant heating, radiant heat zoning, ventilation system
design and operation.
In
February, FSEC returned to Dukane for testing and infrared
evaluation of 3 completed prototype Fortified Homes built
by Dukane’s
sister company, Mustang Construction at Keller Court, Boilingbrook,
IL, just west of Chicago.
Infrared
images were recorded from the inside and outside during
a calm morning with ambient air temperature of about 25 º F and interior temperatures of about
70 º F, and whole house air tightness was assessed
with a blower door test. Whole house infiltration was
ACH50=1.28 (very low) 11 Keller Court data (Specifications,
Table 11) was obtained with a multipoint blower
door test. IR scans found no major infiltration pathways.
Table
11 Dukane Precast’s Fortified Home Specifications |
Component |
Dukane Home |
Conditioned area |
5100 (with basement) |
HERS score |
NA |
Envelope |
Floors and Ceiling |
Precast concrete panels |
Walls |
R-23
(~3") Polyisocyanurate between
precast concrete |
Attic |
Vented with R-38 Polyisocyanurate and
Batt |
Windows |
Insulated glass, vinyl frame, u-value=0.36,
SHGC=0.45 |
Infiltration |
Ach50=1.28 |
Equipment |
Heating |
Radiant floor |
Boiler |
140kBtu, 50 gallon AFUE=92 Gas Boiler |
Cooling |
3 ton, 10 SEER, Unico-type |
Ducts |
High velocity, small ducts, unconditioned
space |
Thermostat |
Programmable |
Ventilation |
Honeywell 150cfm HRV |
Water Heating |
From Boiler |
The ceiling and gable end of the vaulted living room
were built with wood frame construction instead of precast
concrete. Both showed higher heat loss than was generally
found in the precast panels. Flaws in the continuity
of ceiling insulation over the vaulted ceiling were visible
from the vented attic. especially around can lights.
The flat ceilings in this home were insulated with R-38
rigid polyisocyanurate loosely laid on the concrete ceiling
panels. Dukane has now switched to an R-23 precast panel
for ceilings.
Opportunities for Improvement
|
Figure
14 IR-scan
showing metal trusses in precast walls. Temperature
at the crosshairs is 20.2 ° F.
Overlaid temperature graph shows temperature variation
of the surfaces at the white line running horizontally
through the crosshairs. |
Infrared scans were performed on the ranch home and two
other homes nearing completion on Keller Court. All three
had the space heating system in operation holding the interior
near 70 F. Initial scans of the exterior clearly showed increased
heat conduction at the truss locations in the precast panels (Figure
14). The metal truss members are cast into the assembly
to connect the interior and exterior panels and allow for
approximately 3 inches of polyisocyanurate foam (R-23). Exterior
infrared scans showed a 2 - 4º F temperature rise at
truss locations; exterior temperatures were between 12º and
24ºF.
Increased heat loss was also visible at the top and bottom
of precast sections where field connections are made during
construction and filled with grout. Each panel has at least
two lifting fasteners imbedded in the top edge for the crane
to connect to during home construction. Foam insulation around
these fasteners is sometimes removed to connect the lifting
hook and the void is re-insulated in the field. Insulation
levels are reduced where precast walls are connected to floors
and ceilings. These areas have one inch of rigid XPS foam
(R-5) next to the outer panel but are otherwise left open
until structural and electrical conduit connections are made
in the field after which they are filled with grout.
Interior Ducts and Moisture Issues
FSEC Researchers met with Dukane Precast staff, their architect
and mechanical contractor to identify a way to incorporate
interior ducts into a new model of the Fortified House. Ducts
are used primarily for cooling and ventilation as all Dukane
Precast homes are designed with in-floor radiant heat driven
by a high efficiency (92 AFUE) boiler. The boiler also provides
domestic hot water in conjunction with a 50-gallon storage
tank.
The main obstacle to building interior ducts was finding
a place to run ducts from the basement mechanical room to
the first and second floors. Agreement was made to run supply
risers near the center of the home and returns in a chase
on an outside. The two-story foyer offers the best placement
for a central return for both the first and second floor
supplies.
Dukane is currently using a high velocity, small duct air
conditioning system by Unico with 2-inch diameter supply
branches that are easier to fit into walls and chases than
low velocity ducts. One unoccupied home had problems with
condensation accumulating on the attic-mounted ducts. The
cause was traced to humid indoor air contacting cold metal
trunk lines in the vented attic.
No occupant-related moisture was present but the precast
panels, which are still in the process of drying, are one
possible source. Periodic mixing of the indoor air may be
all that is required until moisture output from the panel
is reduced. Otherwise, introducing dry air was recommended
to prevent condensation. Findings and recommendations were
sent of the Dukane Precast in a Trip Report.
- Dye
Company and DelAir - Southern Living Home
Category
A, 1 Home
Category B, 1 Home
Florida
H.E.R.O. met with Dye Company president and his staff to
discuss the new Southern Living Home planned for showcase
at the 2003 Southeast Building Conference (SEBC) in Orlando,
Florida. This firm has a strong desire to differentiate
their homes by emphasizing healthy and energy efficient
homes. Florida HERO introduced the Building America
systems engineering approach to the builder and
subsequent discussions resulted in Dye’s commitment
to partner with Building America in this project.
As a result, researcher met with DelAir mechanical contracting
to discuss the development of mechanical specifications
for the Southern Living project.
This home did have a Honeywell ERV added and had a HERS
score of 88.5. While this home did not meet the BA standard
of performance for the 2003 SEBC show, retrofits were
being completed to bring it up to BA performance level.
The 2004 home achieved a HERS of 89.6. Both homes have
unvented attics with ducts in conditioned space, and
used heat pumps with SEERs ranging from 13.5 - 14.1.
Windows in the 2004 home had a SHGC of .29 and gas (LP)
instant hot water heaters were used.
- EnergyGauge® USA
FSEC - Cocoa, Florida
|
Figure 15 Window input
screen from EnergyGauge USA home energy rating and
simulation software. |
This software
uses the hourly DOE 2.1E engine with FSEC enhancements and
a FSEC-designed user friendly front end to calculate home
energy ratings and energy performance. (Figure 15) Researchers
continue to improve the software’s features and accuracy.
Version 2.0 incorporates many enhancements, which may include
multiple zones, multi-fuel use, and a detailed solar thermal
and solar electric system analysis. For more information,
please visit www.energygauge.com
.
|