|
|
Reference
Publication: McIlvaine, Janet,
David Beal, Neil Moyer, Dave Chasar, Subrato Chandra.
Achieving Airtight Ducts in Manufactured Housing. Report
No. FSEC-CR-1323-03. |
|
|
|
Disclaimer:
This report was prepared as an account of work sponsored by
an agency of the United States government. Neither the United
States government nor any agency thereof, nor any of their
employees, makes any warranty, express or implied, or assumes
any legal liability or responsibility for the accuracy, completeness,
or usefulness of any information, apparatus, product, or process
disclosed, or represents that its use would not infringe privately
owned rights. Reference herein to any specific commercial
product, process, or service by trade name, trademark, manufacturer,
or otherwise does not necessarily constitute or imply its
endorsement, recommendation, or favoring by the United States
government or any agency thereof. The views and opinions of
authors expressed herein do not necessarily state or reflect
those of the United States government or any agency thereof. |
|
Achieving
Airtight Ducts in
Manufactured Housing |
|
|
|
|
Florida
Solar Energy Center (FSEC) |
|
|
Publication
Index:
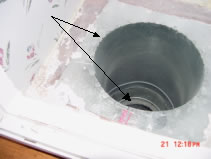 |
Figure
4.
No mastic on return duct in plenum serving packaged heating
and cooling unit. Mastic used elsewhere in the plenum
and throughout house. |
|
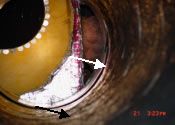 |
Figure
5. Above Misalignment of round duct to round
cutout. Arrow shows where components should mate. Below
Misalignment/insufficient connection surface at round
duct collar to rectangular duct. |
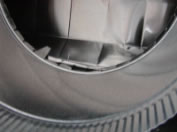 |
Challenges
to Achieving Duct Tightness Recommendations
After
BAIHP makes recommendations in a Trip Report, the factory
staff work out solutions to the problems identified. Often,
problems identified during a test can be quickly located in
other duct systems on the production line. The problems most
often encountered mirror those identified by BAIHP staff during
field work with moisture and air flow damaged manufactured
homes (Moyer, et al, 2001). The most commonly encountered
challenges include:
- Leaky
supply and return(Fig. 4) plenums
- Misalignment
of components (Figure 5), for example, floor boots not reaching
or not being lined up with trunk ducts (in-line floor ducts)
- Free-hand
cutting of holes in duct board and sheet metal without templates,
often with “home made” tools or utility knives
(Fig. 6), for example, a hole for a crossover collar not
being round creates a poor collar connection, holes in trunk
duct for floor boots cut too large for floor riser, creating
a hard-to-seal hole)
- Insufficient
connection area at joints (Fig. 5, bottom), for example,
supply plenum and drop-out collar that are same dimension
as the trunk duct.
-
Mastic applied to dirty (sawdust) surfaces
-
Insufficient mastic coverage
-
Mastic applied to some joints and not others
-
Loose strapping on flex duct connections
-
Incomplete tabbing of fittings (Fig. 7, bottom)
-
Poor tape application
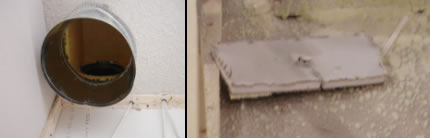 |
Figure
6. Left Holes cut free hand do not mate well
with duct system components. Note round duct is jammed
into an oval shaped cut out. Right Imprecise rectangular
cutout for ceiling register creates poor joint. |
Continue
to Achieving Duct Tightness Recommendations >> |
|
|