Appendix B:
UCF Housing Constructability Lab Annual Report
Progress
Report: April 2003 – March 2004
Prepared for:
The Industrialized Housing Partnership
&
The Building America
Program
Sponsored by:
U.S. Department of Energy
Prepared by:
UCF Housing Constructability Lab
Dr. Michael
A. Mullens, PE
June 15, 2004
Executive Summary
UCF researchers continue to identify and develop prototype
applications of computer technology for the modular factory
floor. Research efforts this year focused on real time production
labor data collection. While labor represents a relatively
modest fraction of production cost, typically 10-15%, it
has a profound impact on operations, including product quality,
cycle time, material waste, and labor productivity. The Status
Tracking and Control System (STACS) is a real time shop floor
labor data collection and reporting system. Production workers
use wireless laser scanners to report their current work
assignment. STACS reporting is web based and provides both
real time manufacturing status and summaries of historical
production performance.
An alpha prototype of STACS was tested in drywall finishing
operations at Avis American Homes (Avis, PA) in Summer 2003.
Test results demonstrated that production workers could operate
the system effectively and that the system accurately captured
scanned activity. Large scale plant-wide testing began at
Penn Lyon Homes (Selinsgrove, PA) in March 2004 and will
continue into Summer 2004. Test results will be used to develop
labor models using linear regression and neural nets.
Trinity Construction Corporation is a large shell contractor
serving Florida homebuilders. Faced with increasing demands
for higher quality, lower cost and more timely delivery,
Trinity is actively exploring innovative alternatives to
conventional concrete block construction, the predominant
homebuilding technology in the central and south Florida
market. Trinity operates a pre-cast concrete panel production
facility, in South Bay, Florida where concrete panels are
pre-cast , transported to the construction site, and quickly
assembled using a construction crane. The UCF Housing Constructability
Lab (HCL) was asked to assist Trinity in improving the current
panelizing process by incorporating lean production principles.
Preliminary research determined that material
handling and rework were primary contributors to the 47%
of labor consumed by non-value added activities. Once started,
the flow of value-added activity was routinely interrupted.
Poor access to materials and tools, rework, ill-defined process
flows, and workforce/1 st line supervision issues were contributing
factors. To address these issues, HCL researchers utilized
lean production principles - challenging non-value added
activities and removing the obstacles to continuous production
flow. Recommendations addressed issues of organization/communication,
structured procedures and work flow, material handling, and
off-line sub-assembly.
To
test the recommendations, Trinity allowed HCL researchers
to perform a 3-day pilot test. The test involved a single
house consisting of 25 wall panels with a gross wall area
of 3,119 ft 2. Productivity increased for all observed
activities, with an average increase of 68%. Not all recommendations
could be realized during the test. Some equipment and personnel
issues could not be resolved on a short-term test basis.
This suggests that the true potential is significantly greater
than that observed during the test – possibly approaching
200% increase in labor productivity. Corresponding cycle
time reductions are estimated to be 20-25%. This successful
pilot test has given Trinity the opportunity to develop a
competitive advantage in the housing construction market
and a good foundation to dominate it.
Innovative Applications of Computer Technology
on the Factory Floor
UCF
researchers continue to identify and develop prototype
applications of computer technology for the modular factory
floor. Research efforts this year focused on the collection
of real time production labor data. While labor represents
a relatively modest fraction of production cost, typically
10-15%, it has a profound impact on operations. Except for
the slower winter months, experienced labor is a scarce resource.
Even if labor is sufficient in the aggregate, it is rarely
positioned where it is most needed at a particular moment
in time. Competitive market pressures are resulting in an
increasing mix of custom home features, increasing the likelihood
of “floating bottlenecks” in production. Quality
and safety can suffer as undermanned crews rush to complete
custom features (i.e., fire-rated walls or a hip roof). If
a crew cannot keep pace, the line slows, production rate
drops, overtime is required and delivery dates are missed.
In
the past, the sheer number of production activities, lengthy
cycle times and extensive product customization have discouraged
manufacturers from accurately estimating labor needs and
using this information to plan and control production.
Instead, they have responded by controlling labor at the
overall plant level, attempting to maintain labor at a historical
target value, which is stated as a percentage of overall
production cost or sales revenue. A limitation of this approach
is that it seldom reflects the actual labor content in the
product, particularly in periods of increasing customization.
To address the problem of shifting bottlenecks, many manufacturers
use flexible resources termed “utility workers”, “flex
workers”, or expeditors. However, the decision to deploy
these workers is often made with minimal planning, after
a problem has started to impact the line.
To better understand the true usage of production labor,
the UCF research team has developed the Status Tracking and
Control System (STACS). STACS is a real time labor data collection
and reporting system designed specifically to meet the needs
of the industrialized housing industry. A schematic of the
STACS system is shown in Figure B1.
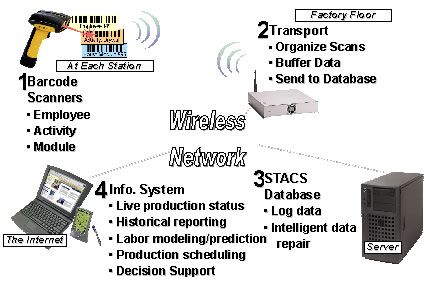
Figure B1 Structure of STACS system
Production workers use
wireless laser scanners to report their current work assignment.
Scanned information is transmitted immediately to a base
station and then relayed to a local shop floor processor,
where it is verified and temporarily staged. Information
is periodically transmitted via wireless LAN to a central
database server where it is stored and used for reporting.
STACS reporting is web based and provides both real time
manufacturing status and summaries of historical production
performance. Real time production performance can be monitored
from the web-based STACS Dashboard (Figure B2).
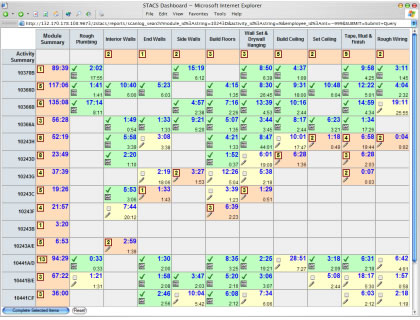
Figure B2 STACS real-time dashboard
“Clicking” on
any item on the Dashboard will display corresponding real-time
details. Historical results can be used for a variety of
analytical and management purposes:
- The development of analytical labor estimating models.
These models can be used to estimate labor requirements
for product costing, production scheduling and labor planning.
- As a baseline for continuous improvement efforts.
|
Figure B3 Scanning drywall
activities
at Avis America |
An alpha prototype of STACS was tested in drywall finishing
operations at Avis American Homes (Avis, PA) in Summer 2003.
Test results demonstrated that production workers could operate
the system effectively and that the system accurately captured
scanned activity (Figure B3). Large scale plant-wide testing
began at Penn Lyon Homes (Selinsgrove, PA) in March 2004 and
will continue into Summer 2004. Test results will be used to
develop labor models using linear regression and neural nets.
Lean Production of Precast Concrete Panels
Trinity Construction Corporation is a large shell contractor
serving Florida homebuilders. Faced with increasing demands
for higher quality, lower cost and more timely delivery,
Trinity is actively exploring innovative alternatives to
conventional concrete block construction, the predominant
homebuilding technology in the central and south Florida
market. Trinity operates a pre-cast concrete panel production
facility, in South Bay, Florida where concrete panels are
pre-cast (Figure B4), transported to the construction site,
and quickly assembled using a construction crane (Figure
B5). The UCF Housing Constructability Lab (HCL) was asked
to assist Trinity in improving the current panelizing process
by incorporating lean production principles.
|
|
Figure B4 Panel forms on forming
bed |
Figure B5 Setting pre-cast concrete
wall panel |
Preliminary research involved extensive observation
and analysis. Value stream mapping identified activities
that contributed value to the customer as well as activities
that added little or no value. Material handling and rework
were primary contributors to the 47% of labor consumed by
non-value added activities. Once started, the flow of value-added
activity was routinely interrupted. Poor access to materials
and tools, rework, ill-defined process flows, and workforce/1
st line supervision issues were contributing factors. To
address these issues, HCL researchers utilized lean production
principles - challenging non-value added activities and removing
the obstacles to continuous production flow. Recommendations
addressed issues of organization/communication, structured
procedures and work flow, material handling, and off-line
sub-assembly. A typical recommended daily production flow
is shown in Figure B6.
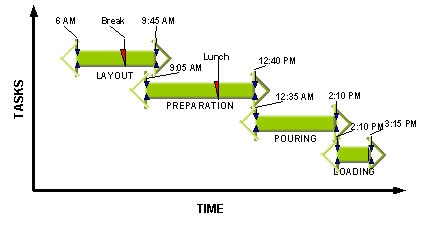
Figure B6 Summary of typical daily
production schedule using continuous flow
To
test the recommendations, Trinity allowed HCL researchers
to perform a 3-day pilot test. The test involved a single
house consisting of 25 panels. The panels had a total of
21 window and door openings and a gross wall area of 3,119
ft 2. The first day was spent organizing and training the
test production team and the second and third days were
dedicated to production. All 25 panels were produced. Productivity
increased (Table B1) for all observed activities. Lifting
productivity was not observed. Conservatively assuming that
lifting will remain at historical levels, overall labor productivity
increased by 47%. If lifting productivity is assumed to increase
at the average rate observed for the other activities, overall
productivity would increase 68%. Not all recommendations
could be realized during the test. Some equipment and personnel
issues could not be resolved on a short-term test basis.
This suggests that the true potential (Table B1) is significantly
greater than that observed during the test – possibly
approaching 200% increase in labor productivity. Corresponding
cycle time reductions are estimated to be 20-25%.
Table B1.
Productivity - ft 2 of wall/ labor hour |
Process
Phase
|
Existing
Process
|
Potential
Process
Results
|
Pilot
Test
Results
|
Productivity
Increase
during Test
|
Layout |
53 |
152 |
91 |
72% |
Prep |
52 |
149 |
79 |
52% |
Pouring |
146 |
211 |
296 |
103% |
Lifting |
75 |
440 |
75* |
0% |
Total |
17 |
49 |
25 |
47% |
The HCL research team recommended that Trinity
proceed with implementation of the lean production recommendations.
In addition to the technical recommendations, the research
team also made recommendations involving worker empowerment,
dealing with the heat and sun, and material/equipment availability.
Potential future research areas include covers for the production
area, on-site factories in new home developments, and factory
installed wall insulation. This successful pilot test has
given Trinity the opportunity to develop a competitive advantage
in the housing construction market and a good foundation
to dominate it.
Publications and Presentations
Mullens,
M. and M. Kelley, “Lean Homebuilding Using
Modular Technology,” Housing and Society: Journal
of the Housing Education and Research Association. In
Press
Mullens,
M. and M. Hastak, “Defining a National Housing
Research Agenda: Construction Management and Production” Proceedings
of the NSF Housing Research Agenda Workshop, Feb. 12-14,
2004, Orlando, FL. Eds. Syal, M., Mullens, M. and Hastak,
M. Vol 2.
Mullens,
M. “Production flow and shop floor control:
Structuring the modular factory for custom homebuilding” Proceedings
of the NSF Housing Research Agenda Workshop, Feb. 12-14,
2004, Orlando, FL. Eds. Syal, M., Mullens, M. and Hastak,
M. Vol 2.
Mullens,
M. and I. Nahmens, “Lean Principles Applied
to Pre-cast Concrete Homebuilding,” Industrial
Engineering Research ‘04 Conference Proceedings,
Houston, May, 2004.
Elshennawy,
A., M. Mullens, I. Nahmens, “Quality-Based
Compensation Schemes for Modular Homebuilding,” Industrial
Engineering Research ‘04 Conference Proceedings,
Houston, May, 2004.
Nahmens,
I., M. Mullens and A. Elshennawy, “The Impact
of Demographics on New Homebuyer Satisfaction,” Industrial
Engineering Research ‘04 Conference Proceedings,
Houston, May, 2004.
Broadway,
R. and M. Mullens, “Shop Floor Information
Systems for Industrialized Housing Production,” Industrial
Engineering Research ‘04 Conference Proceedings,
Houston, May, 2004.
|