|
|
|
Reference
Publication:
Chandra, Subrato, Neil Moyer, Danny Parker, David Beal,
David Chasar, Eric Martin, Janet McIlvaine, Ross McCluney,
Andrew Gordon, Mike Lubliner, Mike McSorley, Ken Fonorow,
Mike Mullens, Mark McGinley, Stephanie Hutchinson, David
Hoak, and Linda Tozer. Building America Industrialized
Housing Partnership, Annual Report - Fourth Budget Period.
04/01/03-03/31/04. |
|
|
Building
America Industrialized Housing Partnership, Annual
Report - Fourth Budget Period |
|
|
Subrato
Chandra, Neil
Moyer, Danny
Parker, David
Beal, David
Chasar, Eric
Martin, Janet
McIlvaine, Ross
McCluney, Andrew
Gordon, Mike
Lubliner, Mike McSorley, Ken
Fonorow, Mike
Mullens, Mark
McGinley, Stephanie
Hutchinson, David
Hoak, and Linda Tozer |
|
Florida
Solar Energy Center |
|
|
|
Article
published in “Automated Builder Magazine,” October
2003.
Zero Energy Manufactured Home
By Michael Lubliner and Andrew Gordon, Washington State
University Energy Program
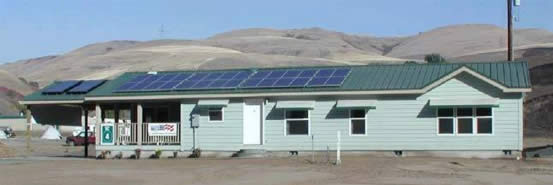
Photo 1. Zero Energy Manufactured Home at the Nez Perce Fish
Hatchery, near Lewiston, ID.
The
nation’s
most energy efficient manufactured home is sited at
the Nez Perce Tribal Fish Hatchery, near Lewiston Idaho.
Construction of the Zero Energy Manufactured Home was
funded by the Bonneville Power Administration, and
coordinated by the U.S. Department of Energy funded
Building America Industrialized Housing Program (BAIHP).
BAIHP researchers worked closely with the Nez Perce
Tribe, Kit Manufacturing (manufacturer) and Clearwater
Homes (dealer).
The goals of the Zero Energy Manufactured Home project were
to demonstrate the technical feasibility of innovative energy
features, and evaluate costs, energy savings and other benefits.
The home is now tribal housing for operations staff at the
hatchery.
Mike
Klingner, general sales manager of Kit Manufacturing, said “[we] felt the project was enlightening in many
ways.” While Kit Manufacturing has experience building
energy-efficient manufactured homes through the Northwest’s
Super Good Cents/Energy Star program, the Zero Energy Manufactured
Home project “took it to the next level. It brought
Kit a greater awareness of energy-efficient building techniques
to those of us who participated in the program.”
According
to the retailer, Christy Skinner, co-owner of Clearwater
Homes, in Orofino, Idaho, the home wasn’t
difficult to install. “There were a few minor differences
in the insulation required between the sections, but it wasn’t
more involved than the average installation.” Clearwater
also installed a second home adjacent to the Zero Energy
Manufactured Home, built to Super Good Cents standards and
identical in layout, but without the additional technologies
used in the Zero Energy Manufactured Home. This home will
be used as a control in evaluating the energy savings in
the Zero Energy Manufactured Home.
In
keeping with the ongoing BAIHP efforts to form partnerships
with builders and suppliers that result in increased numbers
of energy efficient homes, BAIHP staff recruited over twenty
suppliers of innovative energy efficient measures for inclusion
in the Zero Energy Manufactured Home. These measures include:
- Icynene® insulation
in the wall, floor and roof. This expanding foam product
achieves excellent insulating value, has no voids or compression
(common to fiberglass batts) and provides excellent air-sealing.
According to Mike Klingner of Kit Manufacturing, “[Icynene®]
can help to gain higher walls and thinner floors at superior
R-values.” Klinger believes that integrating
the foam insulation into the plant process would make it more attractive and
lower the cost.
- The
solar energy system, consisting of:
- 4.2
kW (28) solar photovoltaic panels, which produce
electricity to the home and/or roll back the meter,
sending power back to the utility grid.
- A “solar-ready” option
package, providing a lower cost, HUD-approved solar
system requiring no roof penetrations. It includes
electrical and plumbing chases for simpler after-market
installation of solar equipment.
- A
closed loop, two-tank solar water heating system,
designed to provide 60 percent of the hot water for
a typical two-bedroom home.
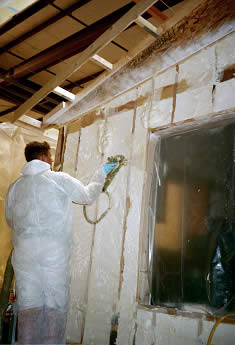 |
Photo
2. Application of Icynene® insulation
on Zero Energy Manufactured Home. |
- Sun-tempered
solar design, which moves existing window area
to the south side, adjustable awnings optimize solar
energy in winter/shade in summer, and insulated
curtains/blinds reduce heat loss/gain.
- Energy
Star© windows,
appliances, exhaust fans, and lighting.
- An
Insider heat pump, with no outside unit, so that no HVAC
contractor is needed. The Insider uses crawlspace air
for heat exchange; since the crawlspace is warmer in
winter and cooler in summer than outside air, heat pump
efficiency is improved.
- A
mastic and screw-in tab-less riser duct system, reducing
branch and trunk duct registers, and resulting in very
low duct leakage and lower material and labor costs.
- R8
crossover ducts, with strong inner liners and plastic
elbows that eliminate duct crimping and ensure proper
long-term airflow.
The solar energy package is expensive, about $30,000. However,
the package is cost-effective today in remote areas where
utility electric service is unavailable or prohibitively
expensive.
The
other upgrades added about $4 per square foot, or approximately
$6,400, to the cost of the house ($47 more per month on a
30 year 8 percent mortgage). Much of this added cost is offset
for homebuyers in lower electric bills, higher resale value,
potential government and utility incentives, and an improved
indoor environment. It is expected that costs will come down
as these technologies become standard or frequently ordered
options.
Testing at Kit Manufacturing and on-site at the hatchery
indicate that the air leakage in the envelope and ducts
of the Zero Energy Manufactured Home are the lowest yet
seen by BAIHP staff. The energy performance of both the
Zero Energy Manufactured Home and the control home will
be monitored over the next year. Results of the monitoring
will help the Bonneville Power Administration, BAIHP staff,
and the manufactured housing identify the cost-effectiveness
and viability of the innovative construction measures.
Project results and updates can be found at: www.bpa.gov/Energy/N/energy_tips/zemh.
For more information, contact Michael Lubliner, WSU Energy
Program, at 306-956-2082 or lublinerm@energy.wsu.edu.
More information on the Building America Industrialized
Housing Partnership can be found at: http://www.fsec.ucf.edu/Bldg/baihp.
|
Disclaimer:
This report was prepared as an account of work sponsored by an agency
of the United States government. Neither the United States government
nor any agency thereof, nor any of their employees, makes any
warranty, express or implied, or assumes any legal liability
or responsibility for the accuracy, completeness, or usefulness
of any information, apparatus, product, or process disclosed,
or represents that its use would not infringe privately owned
rights. Reference herein to any specific commercial product,
process, or service by trade name, trademark, manufacturer,
or otherwise does not necessarily constitute or imply its endorsement,
recommendation, or favoring by the United States government
or any agency thereof. The views and opinions of authors expressed
herein do not necessarily state or reflect those of the United
States government or any agency thereof.
|