Abstract
Before reconstruction can begin after a natural disaster, temporary
housing is essential to stabilization of a community. The
offsite, rapid construction, and the ability to transport (and
relocate) are two advantages of the ruggedized manufactured home. Two
improved specifications, EnergyStar (ES) and
the Building America Structural Insulated Panel (BASIP)
manufactured home, are suggested in this paper that enhance the
energy efficiency, sustainability, and indoor air quality and provide
back up power, without compromising human health, safety or comfort. The
energy performance of the ES and BASIP manufactured
homes are compared to the base case or currently specified ruggedized
manufactured home using the FSEC developed ENERGYGAUGE® USA
(Version 2.5.9) software. The specifications presented in
this paper allow for better quality construction and includes renewable
energy. This not only reduces utility bills during regular operations
but provides electricity and hot water for essential functions
during power outages associated with reconstruction following a
natural disaster.
Introduction
Hurricane Katrina caused major devastation
to parishes, communities and entire cities requiring accommodations
of mass quantities and extreme urgency. The Federal Emergency Management Agency (FEMA) responded
to the temporary housing needs by procuring over 100,000 travel trailers and
over 25,000 ruggedized manufactured homes. However, finding the proper
location and the costs associated with constructing, transporting, installing,
maintaining and operating these temporary housing accommodations has become controversial. Local
governments denied installments within flood zones (which are where most of the
destruction and devastation occurred and where the temporary housing was needed)
and local citizens brought opposition citing that they feared these “FEMA
Cities” would increase crime rates and lower their property values. Critics
believe that dispersing the money they spent per home, directly to each of the
victims they provided accommodations to, is a better use of taxpayer dollars
than purchasing these units for temporary and often, one time only, use. While
the temporary housing program is antiquated, it is what the law
allows.
FEMA procured manufactured
homes are used to accommodate victims of natural disasters. As
hurricanes are predicted to intensify and increase in numbers,
more temporary structures will be needed. When Hurricane
Katrina struck the shores of Louisiana, Mississippi and Alabama
last year, 25,000 manufactured homes and 100,000 travel trailers
were ordered (and built) to help accommodate the thousands of victims
who could not find and/or afford safe housing while their homes
were being repaired or in some cases, rebuilt completely. By
extrapolating information from recent articles, the costs associated
with recent manufactured home and travel trailer purchases amounts
to approximately 2.9 billion dollars. Each travel trailer
costs about $10,000. Each manufactured home costs about $76,800
per dwelling, which includes purchase, transportation, installation,
maintenance, cleaning and disposal. However, these figures
do not include energy costs and environmental impacts, associated
with the manufactured homes that are currently used.
Continued to be scrutinized for temporary home expenditures,
FEMA is complying with what
law allows. The
Stafford Act limits the amount of money FEMA can grant
directly to an individual at $26,200. While
this may seem like adequate funds to support a household
for a period of 18 months, some times, as experienced
during Hurricane Katrina, safe housing accommodations
are not available because an entire community has been
devastated. The program for providing ruggedized
manufactured homes was developed in the 70’s
and although antiquated, the
program or procurement specifications warrant improvement.
Manufactured homes, utility expenses, maintenance,
etc. are provided at no cost to the victims until they
can move back into their existing homes or find other
permanent housing. The
manufactured homes are typically provided for a period of not more
than 18 months. Once the 18 month period has expired, the manufactured
homes are vacated and immediately transported to a staging area for
future reuse or sale through the GAS website (http://gsaauctions.gov/gsaauctions/gsaauctions). If
displaced residents can not find affordable housing, extensions are
granted by FEMA. Most recently, the Punta Gorda, FL village
has extended the remaining occupants’ stay until September
2006, totaling a 24 month housing period for these residents. In
Florida there are 4,160 manufactured homes or trailers still occupied
by storm victims, down from a 2004 peak of more than 17,000. There
were 551 families at one time in the Punta Gorda village that opened
in November 2004 (see photo of typical FEMA temporary community,
the one pictured in Figure 1 is in Arcadia, FL).
The procurement process that FEMA initiates when manufactured
home orders are needed, start with FEMA requesting
quotes
from manufactured home builders to build the homes
in accordance with HUD Manufacturing Housing
Standards,
also known as Title 24 (Chasar, et al. 2004). The
manufactured homes specified to these standards,
developed
in the 70’s,
are often constructed to the minimum standards, resulting in large
energy use compared to their site built equivalents. The specifications
recently used in hot and humid climates (i.e. areas where Hurricane
Katrina struck) have the potential for indoor air quality and high
maintenance concerns, in addition to high energy use. Poor
indoor air quality can induce medical complications in occupants
with asthma or other chronic illnesses and with energy costs on the
rise, procurement specifications necessitate energy efficient solutions
without compensating human comfort or safety.
If FEMA’s current
procurement process is to remain standard procedure, this report
recommends two specifications for consideration. The EnergyStar Ruggedized
Manufactured Home (ES) and the Building America Structural
Insulated Panel Manufactured Home (BASIP) specifications,
included in this report, provide improved temporary shelter accommodations
suitable for multiple moves, and have capabilities to provide power
for essential loads during extended power outages. Not only
are the tangible benefits associated with energy cost savings the
justification for this report, but indoor air quality plays and
increasingly demanding role amongst occupants with sensitivities
to asthma and other environmental related health conditions. Also
included in this report are energy cost comparisons and analysis.
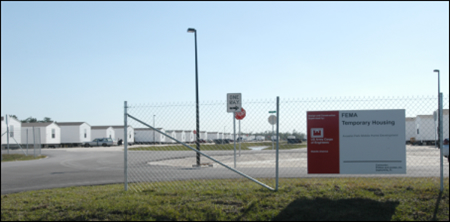
Figure 1. FEMA City, Arcadia, FL
Photo Credit: FEMA
The ES manufactured home specification is modeled from
the Energy Star guidelines for manufactured homes (MHRA 2003). An
ENERGY STAR labeled manufactured home must be at least 30% more
energy efficient in its heating, cooling and water heating than
a comparable home built to the 1993 Model Energy Code (MEC) (Chasar,
et al 2004).
The
specification
for BASIP goes
a little further in creating a
specification that results in optimal indoor air quality, increased
energy savings and also provides “free
energy”. Table
1 summarizes the window,
and surface U values as well as other characteristics.
Table 1. Summary of Construction
of the Existing and Proposed
Specifications for FEMA
Ruggedized
Manufactured Homes
Characteristic |
Base Home
(existing) |
Energy
Star (proposed) |
BASIP
(proposed) |
Floor Insulation |
R-19 |
R-21 |
R-19 |
Wall Insulation |
R-13 |
R-13.5 |
>R-15.4 |
Ceiling Insulation |
R-21 |
R-18.5 roof deck
radiant barrier |
>R-23 |
Roof |
Dark Shingle |
Light shingle
with radiant barrier |
White metal raised
seam roof |
Windows |
Single Pane, Metal
Frame |
Low-E Vinyl; Frame |
Low-E Vinyl Framed
with storm shutters |
Heating System |
Electric Resistance
Furnace, COP:1 |
Heat Pump HSPF
7.5 |
Heat Pump HSPF
7.7 |
Cooling System |
Central Air (Split
System) Conditioning SEER13-2 ton |
Wall Hung Heat
Pump SEER 13-2 ton |
Wall Hung Heat
Pump SEER 13-1.5 ton |
Water Heater |
Electric Water
Heater 40 gallon capacity |
Electric Water
Heater 40 gallon capacity |
ICS Solar Water
Heater with backup 40 gallon electric water heater |
Ventilation System |
Under floor |
Above ceiling
in vented attic |
Under SIP roof
( in conditioned space, unvented attic) |
Duct Joints (leakage expressed
as CFM25 to out as % of floor area) |
Industry Standard – 6%
leakage to out |
Sealed with mastic – 3%
leakage to out |
Sealed with mastic
(inside thermal envelope) 0% leakage |
House air tightness (in terms
of ACH50)* |
7.5 |
5.10 |
4.00 |
Retractable Awning |
N/A |
Optional (provides
additional square footage/outdoor space) |
Optional (provides
additional square footage/outdoor space) |
On Site Generated Power |
N/A |
N/A |
3.25kW PV system |
*Figures
from measured data of blower door test of US manufactured housing
(Baechler, et al, 2002)
Base Case,
Energy Star and Building America Structural Insulated
Panel Manufactured Home Characteristics
Improving the construction methods
and energy efficiency of federally procured ruggedized manufactured
homes, used as temporary accommodations, will increase the durability
and expand the life expectancy and reusability. The improved
specifications and revised roof layout of the BASIP will
also accommodate a mating of “single
wide” units to make a “double wide” and larger
unit that would provide a more comfortable environment and a more
mainstream approach to typical home floor plans (see end wall elevations
as illustrated in Figure 3). This
report does not explore floor plan redesign at this time; however
it does identify some of the few designs that have evolved since
Hurricane Katrina left so many victims homeless.
The base case or currently
procured and the proposed ES ruggedized manufactured home
have overall dimensions of 14’x 60’ (Figure 2). The
units specified have 3 bedrooms and 2 baths. The base case and ES units
have ventilated attics and gabled roof plans (Figure 3). The BASIP unit
has been lengthened to
accommodate a mechanical room and mono-sloped roof (Figures 4 & 5).
The ES specification
uses an advanced framing method. While the base case uses
typical 2x4 stud construction spaced on 16” centers, the
advanced framing method uses 2x6 studs spaced on 24” centers. Advanced
framing methods may reduce wood use up to 25% and improve wall
thermal resistance values from 5 to 10%. It can also decrease
labor with fewer pieces going together, therefore saving
money. The BASIP specification
uses structural insulated panel method with integral wire chases
for walls and the roof but the floor system uses advanced framing
method, locating the plumbing requirements in the “belly”,
as does the base case and ES.
The BASIP specifies
a photovoltaic (pv) integrated metal roof system with a skylight
and Integrated Collector Storage (ICS) solar hot water system. The
elevations illustrate “Bahama” style shutters that
provide hurricane protection and solar shading. The end
wall elevation (Figure 5) illustrates the inclusion of a retractable
awning that also provides solar shading and additional square
footage.
Energy
Analysis Using EnergyGauge®
The proposed specifications and
the base case federally procured manufactured home are analyzed
using the FSEC developed ENERGYGAUGE® USA (Version 2.5.9) software program.
This program predicts building energy consumption using the DOE2
analysis engine with a user friendly front end that develops DOE2
input files and models that are more appropriate for residential
building systems (Parker, et. al, 1999).
An analytical model
was developed for each of the manufactured home specifications. These
models were essentially the same with differences only in the R-values
in the various building envelope components, the duct leakage values,
the heating and cooling equipment, fenestration properties and
the integration of renewable energy sources, i.e. pv and solar
hot water heating. The
base case and ES are similar in geometry but differ in
hvac systems engineering and hvac equipment location.
Considering the energy
costs alone, these specification recommendations facilitate significant
utility demand reductions. During a 12 month period, the
latest order of 25,000 FEMA specified ruggedized manufactured homes
will consume about 250 GWh, which will cost the Federal Government
approximately 32.55 million dollars (at $0.13/kWh). If these
units were deployed to other areas like Hawaii, where utility rates
are almost 44% higher, the government’s electric bill could
cost over 46 million dollars. The ES, which proposes
to improve the energy efficiency by at least 14%, would provide
a savings of over 4.5 million dollars over a 12 month period. The BASIP, proposes
to improve the efficiency by at least 78% (see Table 2). This
equates to about 19.5 GWh of electricity saving approximately 25.4
million dollars.
The ES manufactured
home would eliminate approximately 23,500 tons of greenhouse gas
emissions, equivalent to removing 3,815 passenger cars and light
trucks from the highway for one year or saving our reliance on
49,595 barrels of oil. The BASIP specification would
remove approximately 119,000 tons of greenhouse gas emissions,
equivalent to removing 19,318 passenger cars and light trucks from
the highway for one year or saving our reliance on 251,134 barrels
of oil.
Table 2. Summary of Comparisons of Simulated
Savings
End-Use |
Base
(existing) |
Energy
Star
(proposed) |
% Savings
Over Base |
BASIP
(proposed) |
% Savings
Over Base |
Annual Energy Use (kWh) |
10,017 |
8,622 |
14 |
*2,189
(6,161 total) |
78 |
Annual Energy Costs ($) @ $0.13/kWh |
1,302 |
1,122 |
14 |
286 |
78 |
Annual CO2 Output
(tons) |
5.85 |
4.91 |
16 |
1.09 |
81 |
AC |
2,181 |
1,652 |
24 |
1,458 |
33 |
Heat |
1,316 |
373 |
72 |
487 |
63 |
Hot Water |
2,768 |
2,652 |
4 |
**1,346 |
51 |
Lighting |
1,111 |
1,111 |
0 |
479 |
57 |
* Net Energy Usage = Total Energy Usage – PV Produced (see
Figure 7 for details)
** This figure differs from figure in Appendix B (page B12) to include additional
energy
usage during the freeze protection months of December, January and February)
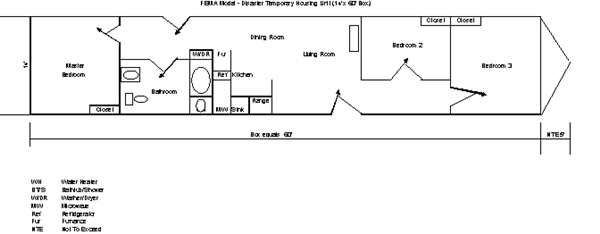
Figure 2. Floor plan for
the Base Case (Courtesy of Palm Harbor Homes)
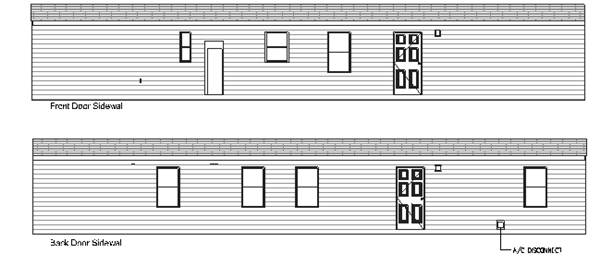
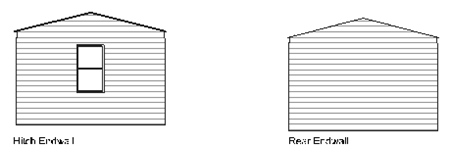
Figure
3. Elevations for the Base Case (Courtesy of Palm Harbor Homes)
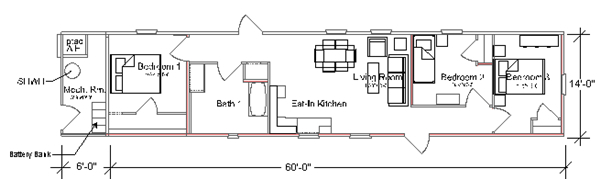
Figure
4. Floor plan (by Palm Harbor Homes, et al.) for the Energy Star
&
Building America Structurally Insulated Panel Manufactured Homes
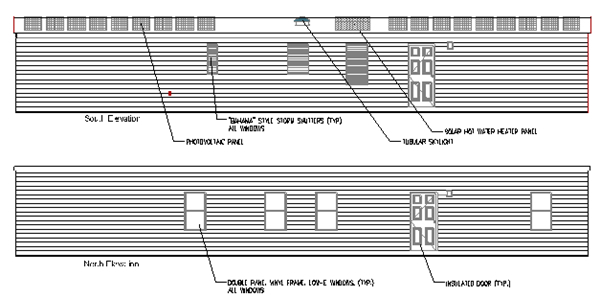
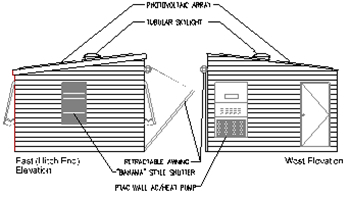
Figure
5. Elevations for the Building America
Structurally
Insulated Panel
Manufactured Home
Inegrated PV Array
The BASIP specification
proposes the integration of a 3.25kWp pv array that would generate
the peak power requirements. This is especially beneficial
when manufactured homes need to be deployed to areas where utilities
have not been restored or during times when service is interrupted. EnergyGauge® models
the annual energy use and the annual energy produced by the pv
array for the home located in New Orleans, LA. Figure 6
illustrates the summary of monthly averages and Figure 7 illustrates
the summary of hourly averages. The pv array produces a
net energy of 4,224 kWh. Total consumption is 6,413 kWh annually
for a net energy use of 2,189 kWh and 78% savings. If the
pv array was omitted, the BASIP would produce 38% savings over
the base case manufactured home.
|
|
Figure 6. Monthly electrical
consumption and production. |
Figure 7. Hourly
summary of electrical
consumption and production |
Figure 8 demonstrates the average hourly electrical uses for the
whole year, revealing the hvac and hot water require the largest
demand (which is also typical in the base case and ES models).
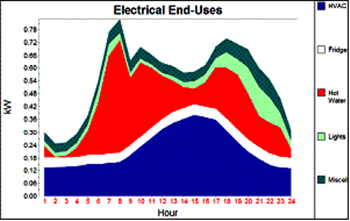
Figure 8. BASIP manufactured home
electrical end uses.
HVAC
The
base case manufactured home as it is constructed today uses a
mechanical system that is ducted under the floor of the home
(referred to as “in the belly”). The air handling
equipment is in the interior of the home and the compressor is
set onto a concrete pad once the manufactured home is delivered
to the site. This requires coordination and additional
personnel to connect the system on site and also almost never
involves any commissioning or verification that the system is
functioning properly as designed. The ES manufactured
home models an improved hvac system with higher energy efficiency
and improved requirements on duct sealing. It also relocates
the ductwork above the ceiling, as does the BASIP. However,
the BASIP creates a conditioned space for the ductwork
due to the sip system. The relocation of ductwork above
the ceiling eliminates the risk of supply vents being covered
with furniture. The BASIP uses the plenum above
the ceiling and below the sip for return air supply (see Figure
9). This may create an example where innovative technology
precedes code development because flame spread ratings and fire
code issues may need to be investigated further to ensure code
compliance.
The BASIP specification
proposes a hvac system that is installed onto the home in the factory,
allowing the mechanical system to be completely operational upon
delivery. The BASIP also properly sizes the unit
with respect to its characteristics, allowing proper humidity removal
and better indoor air quality.
The energy savings
from the improved air conditioning and heating demands amount to
44% and 45% for the ES and BASIP respectively
over the base case. The BASIP can credit this savings
so the increased energy efficient rating and the properly sizing
of the system. The SIP, in addition to tight ducts, results
in tighter construction, less leakage and better indoor air quality.
Domestic
Hot Water
The BASIP manufactured
home specifies an Integral Collector Storage (ICS) hot water system
which saves about 50% energy over the base case and ES home
(see Figure 10). In the ICS, the hot water storage system
is the collector. Cold water flows progressively through the collector
where it is heated by the sun. Hot water is drawn from the top,
which is the hottest, and replacement water flows into the bottom.
This system is simple because pumps and controllers are not required.
On demand, cold water from the house flows into the collector and
hot water from the collector flows to a standard hot water auxiliary
tank within the house (Harrison, et. al, 1997). The benefit
to using an ICS system over a drain back system is less mechanical
parts and pumps. The BASIP unit
will have a user’s manual and diagrams installed at the water
heating system (located in the mechanical room, see Figure 3) that
indicate freeze protection procedures during the months of December,
January and February, as well as during transportation and relocation. Another
benefit of using an ICS system is the availability of hot water
during power outages.
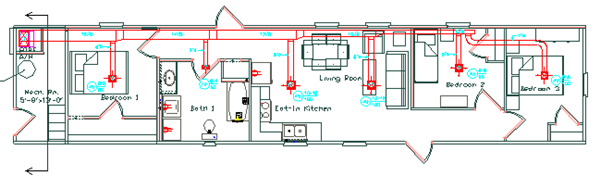
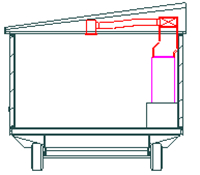
Figure 9. BASIP cross section and HVAC Layout
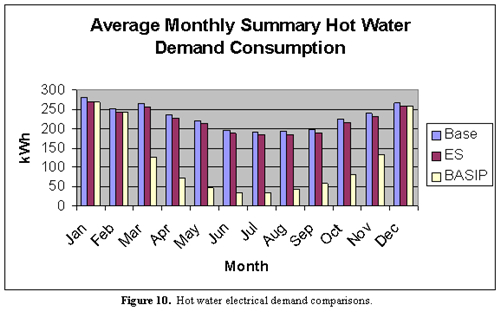
Peliminary Economics
Early in the research
of this report, incremental cost estimates were generated for the ES manufactured
home of about $900. However, due to the proposed wall mount
hvac system, third party mechanical system installation costs are
omitted (and for each relocation). These
charges are estimated at $700 per move. Table 4 estimates
incremental costs per component and assumes two moves. This
results in a net savings of approximately $854 over the base case,
including other proposed upgrades. The
proposed BASIP manufactured
home specifications have incremental costs associated with the
skylight, pv, solar hot water system, high efficiency hvac system
and sip construction. The
pv array is a large incremental cost in the BASIP manufactured
home specification. Systems can generally costs about $10K
per kW of pv array. This
would amount to approximately $32.5k for the specified BASIP system.
Optimistically and with bulk pricing for many of these systems
purchased, the array could be procured as low as $6 per kW or about
$20k (the figured used in Table 3). Another
large incremental costing component is the ICS hot water system. This
is estimated at a $2,300 up charge from the typical electric water
heaters, which cost about $200. The other incremental costs
in Table 4 are likely much higher than would be actually realized
due to the experimental nature of the proposal. With these
caveats understood, Table 4 illustrates the incremental costs,
energy savings and simple payback periods for each specification. The
life cycle costs will be determined at a later date if the scope
of this project warrants such investigation. Note that the
savings and paybacks will vary in accordance with the home’s
location in respect to the utility rates.
Table 3. Incremental Costs Comparisons
and Savings
|
Incremental
Cost |
Incremental
Cost
($/ft2) |
Electric
Rate
($) |
Energy
Savings
(kWh/day) |
Annual
Energy Savings
($) |
Simple
Payback
(yrs) |
Annual
Life Cycle Costs/yr |
ES Home |
($854) |
($1.04) |
$0.13/kwh |
$4.27 |
$201 |
- |
$3,670 |
BASIP Home |
$27,301 |
$29.55 |
$0.13/kwh |
$21.59 |
$1,023 |
27 |
$3,649 |
Table 4. Component/Incremental Cost Estimates
for ES & BASIP
|
ES Home
Component |
ES Home
Component
Cost Increment |
BASIP Home
Component |
BASIP Home
Component
Cost Increment |
HVAC (equipment) |
Wall hung AC/HP,
SEER 13 |
$101 |
Wall hung AC/HP,
SEER 13 |
$101 |
HVAC Labor (based on
2 moves) |
Negative cost due
to equipment attached to unit |
($1,400) |
Negative cost
due to equipment attached to unit |
($1,400) |
Framing |
Advanced framing,
less material, less labor |
$0 |
Sip (walls & roof) ±$3.25
square foot |
$2000 |
Windows |
Vinyl frame, dbl.
pane, low-e |
$400 |
Vinyl frame, dbl.
pane, low-e |
$400 |
Roof |
Light colored asphalt
shingle |
$0 |
White, raised
seam, metal roof |
$2,200 |
Floor Plan |
N/A |
N/A |
Lengthened floor
plan |
$700 |
Jump Duct |
Jump duct for return
air from wall hung at end of unit |
$45 |
n/a |
n/a |
Retractable awning |
Optional |
N/A |
12’w x 10’d |
$300 |
Bahama shutters |
N/A |
N/A |
See figure 4 |
$400 |
Skylight |
N/A |
N/A |
(1) skylight 18sq.ft. |
$200 |
Solar Hot Water |
N/A |
N/A |
ICS w/aux. elec.
tank |
$2400 |
PV system |
N/A |
N/A |
3.25kW array |
$20,000 |
Total Incremental Cost |
|
($854) |
|
$27,301 |
Conclusions
Through various programs that the federal government has initiated,
the search for more affordable, energy efficient and sustainable
temporary housing is taking a more aggressive stance in the building
environment. When FSEC was tasked by DOE to develop a proposal
for improved specifications for FEMA, we sought input from various
industry partners to discuss different ways to improve the current
FEMA specifications. This included manufactured home building
personnel, material manufacturers, building science researchers
and others. FEMA personnel was contacted on numerous occasions
but declined to comment. These discussions along with several
published reports formed the basis for the proposed recommendations
in this report. One such published report was a site visit
conducted by a member of the Building America Industrialized Housing
Partnership and others affiliated with manufactured housing industry
in September of 2004. The report discloses possible moisture-related
problem areas and made recommendations for manufactured homes built
for FEMA and destined for Hurricane Charley victims. The
largest problem areas were the vapor barrier placement, duct leakage
and oversized hvac systems (Chasar, et. al. 2004). In July
of 2000 the first HUD-Code home made of structural insulated panels
(SIPS) was tested, instrumented and monitored for energy efficiency
(Baechler, et al., 2002). The results of this experiment
provided the premise from which the BASIP was developed.
The FEMA procured manufactured
homes are currently constructed in accordance with the Housing
and Urban Development’s manufactured housing standards
(the HUD code). While there are many examples of high quality
and cost effective manufactured homes, the FEMA minimum standard
homes can consume more energy than their site built comparatives
and use materials and mechanical systems that can potentially contribute
to poor indoor quality and low durability. Two improved specifications
are presented in this report to enhance energy efficiency, sustainability,
indoor air quality and provide back up power, without compensating
human health, safety or comfort, for high performance ruggedized
temporary housing.
Imagine the headlines
revised from “The Land of 10,770 Empty FEMA Trailers” (Figure
11), to “10,770 Zero Energy Trailers Provide Power for Small
Community”. If these units had been built with the BASIP specifications,
they could generate enough power to provide basic power necessities
of a small parish. With more and more headlines like “FEMA
Homes Stranded in NC”, “Thousands
Still Waiting for FEMA Trailers”;
how does FEMA justify the process for temporary housing? Placing
manufactured homes into communities affected by natural disasters,
such as Hurricane Katrina has met enormous resistance by neighboring
communities, as well as, local officials. “The NIMBY
(not in my backyard) effect goes beyond the Big Easy itself: Half
of Louisiana's parishes have banned new trailer parks”. The
Punta Gorda FEMA Park (largest-ever trailer park) has received
accusations about drug dealing, domestic abuse, theft and vandalism. Despite
those concerns, some believe extraordinary events require extraordinary
cooperation.
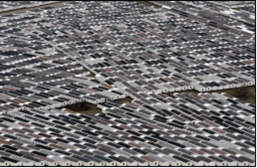
Figure 11. More than 10,000 trailers were sitting
at the airport in Hope, AR
(AP Photo by Danny Johnston)
The proposed specifications still need further investigation with
regards to code exceptions and/or exemptions and fire resistance
compliance due to innovative technologies that have evolved since
the development and implementation of the HUD Code. Space
planning and overall layout should also be examined further. While
this report does not explore floor plan redesign at this time,
it does identify a few designs that have evolved since Hurricane
Katrina left so many victims homeless. Hurricane Katrina
brought about many design charettes and discussions by architects,
developers, politicians and manufactured housing executives. We
can even look historically at measures taken after the San Francisco
earthquake of 1906 left thousands homeless and over 5,600 “temporary
cottages” were built (see Figure 12).
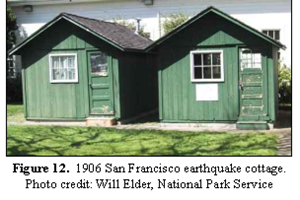
The
consensus is that affordable, temporary housing needs to take on
a new shape and mission. The U.S Department of Energy's Office
of Energy Efficiency and Renewable Energy Department’s
annual Solar Decathlon, a competition to design, build, and operate
the most attractive and energy-efficient solar-powered home, displays
examples every year of self sufficient innovative homes, that have
been transported to the Mall in Washington D.C. Regardless,
Hurricane Katrina has proved that a new process and strategy is
in need, one that is healthy, sustainable, and reusable and before
an energy crisis hits home again, and one that is energy efficient
and responsible.
References
- Code of Federal Regulations Housing and Urban Development [HUD],
Manufactured Home Construction and Safety Standards, 24, Part
3280, US Government Printing Office, 1999.
- Baechler, M.; Lubliner, M; Gordon, A (2002). “Pushing
the Envelope: A Case Study of Building the First Manufactured
Home Using Structural Insulated Panels” Proceedings of
ACEEE 2002 Summer Study, American Council for an Energy Efficiency
Economy, Pacific Grove, CA.
- Chasar, D., Moyer, N., McIlvaine, J., Beal, D. and Chandra,
S., "Energy Star Manufactured Homes: The Plant Certification
Process," Proceedings of ACEEE 2004 Summer Study, American
Council for an Energy Efficient Economy, Washington, DC, August
2004.
- Harrison, J., Tiedeman, T. “Solar Water Heating Options
in Florida”, Florida Solar Energy Center, Cocoa, FL, FSEC-EN-9,
May 1997
- McGinley, W. M., “Study of Innovative Manufactured Housing
Envelope Materials”, Final Report to the Florida Solar
Energy Center, Under the Building America Industrialized Housing
Partnership, April 2002.
- Moyer, N., Beal, D., Chasar, D., McIlvaine, J., Withers, C.,
and Chandra, S., “Moisture Problems in Manufactured Housing:
Probable Causes and Cures,” Proceedings of ASHRAE
Conference IAQ2001, American Society of Heating, Refrigerating
and Air-Conditioning Engineers, Inc., Atlanta, GA, August
2001.
- Parker, D. et al, 1999. "Energy Gauge® USA: A Residential
Building Energy Simulation Design Tool", Proceedings of
Building Simulation ’99. International Building Performance
Simulation Association, Organizing Committee for the 6th International
IBPSA Conference, Department of Architecture Texas A&M University,
TX.
Acknowledgement
This work is sponsored,
in large part, by the US Department of Energy (DOE), Office of
Energy Efficiency and Renewable Energy, Building Technologies Program
under cooperative agreement number DE-FC26-99GO10478. This support
does not constitute an endorsement by DOE of the views expressed
in this report.
The authors appreciate
the encouragement and support from Bert Kessler (Palm Harbor Homes),
Bill Wachtler (Structural Insulated Panel Association), Bill Chaleff
(Chaleff & Rogers, Architects), Janet McIlvaine (Florida Solar
Energy Center), Danny Parker (Florida Solar Energy Center), Eric
Martin (Florida Solar Energy Center), Dennis Stroer (Calcs Plus),
Michael Lubliner (Washington State University), Michael Baechler
(Pacific Northwest National Laboratory), Mike Dalton (Polyfoam),
Ron Sparkman (Barvista Homes), John Michael (ATEX Distributing). |